The National Institute of Advanced Industrial Science and Technology (AIST) and OMRON Corporation have jointly developed a film-type vibration device that is just seven micrometers thick, making it the thinnest in the world and also the lightest. The device, which utilizes ultrathin micro-electro-mechanical systems (MEMS) technology, will reportedly be useful for expressing a variety of tactile sensations on PC keyboards, game console controllers, medical devices and other equipment.
Eccentric motors or "piezoelectric ceramics" that convert energy and electrical signals into movement are commonly used as actuators for realizing "haptics," the technology of conveying tactile sensations through force, vibration, movement and so on. Although these are used in smartphones, game console controllers and other devices, because of issues with their flexibility and size it is difficult to attach them to curved surfaces or to create arrays by arranging several of them in a line. The tactile sensations they are capable of expressing are limited due to their slow start-up times and because they only offer on/off control.
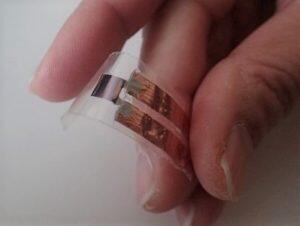
The device developed by AIST and OMRON is a piezoelectric thin-film actuator for use in haptics. It brings together reaction speed, power and flexibility as a result of making the piezoelectric ceramic ultrathin. The multilayer construction comprises silicon, metal electrode thin film, piezoelectric thin film and insulating film. In terms of size, it is a five-millimeter square and is seven micrometers thick. When subjected to a direct current the actuator as a whole bends, and when subjected to an alternating current it vibrates. It is as flexible as aluminum foil, allowing it to be affixed along a curved surface even when mounted on a film substrate.
In order to ensure that the actuator's vibrations are conveyed well, AIST and OMRON also devised a material for pasting the actuator and film substrate together. When a haptics film that they produced is subjected to a current of 10 volts, vibrations with an amplitude of 11 micrometers are obtained, amply exceeding the lower limit of one micrometer that can be detected on a fingertip.
The haptics film was produced by arranging these actuators in a 2 x 2 tile formation to create a four-actuator array. This film was then tested by making it vibrate according to different patterns and determining how well the respective vibrations could be identified through the sense of touch on a fingertip. 97.5% of the individuals tested could accurately detect a pattern in which the four actuators were simultaneously switched on and off repeatedly at half-second intervals. On the other hand, that percentage fell to a level of around 50% when the pattern involved two adjoining actuators being alternately switched on and off repeatedly. This is believed to be because the vibrations from the on actuators were too strong and ended up being felt in the location of the off actuators.
Toshiro Takeshita, a research fellow at AIST's Sensing System Research Center, which was part of the development group, explains that, "The problem did not involve the actuator itself, and it could likely be resolved by adopting a structure that separates the vibrations on the film side. There is also room to improve the frequency of the vibrations and how the voltage is applied."
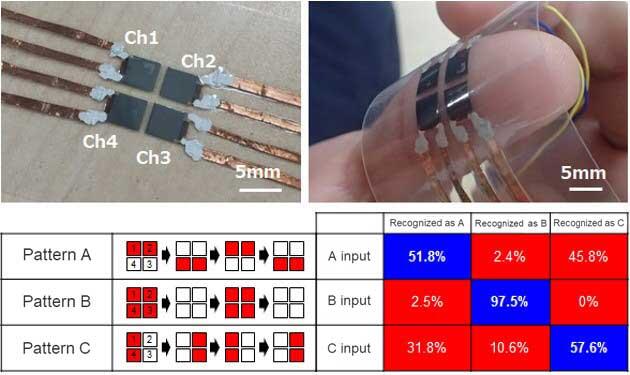
Going forward AIST and OMRON will aim to express a variety of tactile sensations by forming arrays that use an even larger number of actuators, for example. Mr. Takeshita explains that, "It is quite a thin device, and its durability poses the biggest challenge. In addition to being installed on PC keyboards, mice and game console controllers, we anticipate it will be employed in a diverse range of electronic equipment including in remote medicine for conveying the force that surgical robots are exerting to doctors, and for healing and relaxation purposes.
The results were announced verbally on January 29 at MEMS 2021, the Institute of Electrical and Electronics Engineers' (IEEE) International Conference on Micro Electro Mechanical Systems, which was held online due to the coronavirus pandemic.
Original article was provided by the Science Portal and has been translated by Science Japan.