The manufacturing process for products of the electronic industry, such as semiconductors, flat panel displays, and solar batteries uses dangerous toxic and flammable gases, such as silane and hydrogen. Currently, to safely detoxify these gases, a thermo-oxidative reaction in which the gases are heated to more than 1000 °C and then decomposed is mainly used. However, previous development of the detoxification method was limited to improving efficiency and reducing wasted energy, such as from heat dissipation, so the development of new technology that can realize energy savings is an important issue.
Development for this problem was entrusted to Kanken Techno Co., Ltd. (Nagaokakyo City, Kyoto Prefecture) through A-STEP, a research project run by JST. Kanken Techno Co., Ltd. is developing a device that can achieve high efficiency and low-energy detoxification of dangerous gases, based on the research results of Professor Takanori Ichiki of the University of Tokyo Graduate School of Engineering. The development team focused on the fact that the lower explosion limit depends on the pressure of the gases used and examined conditions where the ratio of dilution gases used could be reduced. By reducing the pressure within the pipe from the pump outlet of the device manufacturing equipment, to the exhaust gas abatement device, they created an environment where the lower explosion limit was increased and no chemical reaction occurred. In addition, in using arc plasma, which is normal generated in atmospheric pressure, as the heat source, they discovered the optimal conditions for its stable generation in a reduced pressure state of approximately 0.1-10 kPa.
Through this development it was made possible to perform detoxification processing by thermally reacting the dangerous gasses with oxygen, using arc plasma as a heat source, within a gas abatement device in a reduced pressure state. Since dilution using nitrogen is no longer necessary the amount of energy required has been reduced by up to 75% when processing silane gas. The developed system can be applied to other exhaust products containing flammable gases through optimizing the processing conditions without altering the devices' structure. This has the potential to be applied to devices involved in products that rely on hydrogen in their manufacturing process, such as silicon wafers and other products.
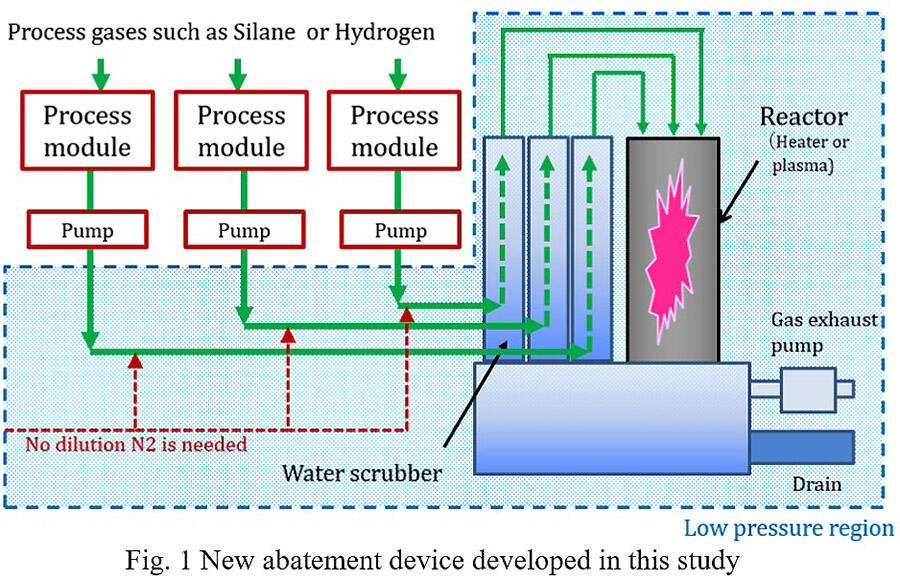