On June 17, the New Energy and Industrial Technology Development Organization (NEDO) confirmed that pharmaceutical manufacturing facilities using a new batch-continuous production system as part of the "Strategic Energy Saving and Technical Innovation Program" theme-setting business cooperation scheme are expected to reduce energy use by about 80%. This is in comparison with conventional main systems in production systems under development. NEDO also said that the system might cut waste by 30-40%. Production and trialing of the prototype will now be conducted with the aim of creating production facilities that contribute to energy saving as well as more efficient production and resource use in Japanese pharmaceutical manufacturing.
The reconfigurable, modular, pharmaceutical production facility "iFactory" employs a batch-continuous production method combined with a continuous synthesis method instead of the conventional batch-type manufacturing method. It is being developed by nine partners as part of a NEDO project: Takasago Chemical, Mitsubishi Tanabe Pharma, Konica Minolta, Yokogawa Solution Service, TEC Project Services, Taisei Corporation, Shimadzu Corporation, Mitsubishi Kakoki, and the National Institute of Advanced Industrial Science and Technology.
The domestic market for pharmaceuticals in Japan was ¥11.5 trillion as of 2015, but it is forecasted to reach ¥25.7 trillion by 2030. Many of the high-function chemicals used in these pharmaceuticals, both domestically and internationally, are produced using a batch production method in which all raw materials are put into a reactor, and the product is extracted after all physical reactions are complete. However, there is a growing need to reduce waste and CO2 from manufacturing and to switch to "on-demand production" that produces "only what is needed when it is needed." In response to this need the development of iFactory commenced as part of a NEDO project in FY2018.
Previous tests on three pharmaceutical/fine chemical-related items manufactured in a batch-continuous process have confirmed that cleaning, concentrating, crystallizing, and filtering allows for eight hours of continuous operation at a production rate of 10 kg/h. In addition to this, by making the "filtration" production step continuous, it is possible to save the equivalent of 78% of energy used during eight hours of operation compared to general batch-type equipment. Similarly, continuous-type equipment introduced into the reaction process using a continuous reactor can attain an 84% reduction. Furthermore, the drastic reduction in the use of cleaning solvents and in the frequency of replacement achieved through the continuous process is expected to reduce waste by 30-40% for these three pharmaceutical/fine chemical-related items compared to when manufactured using the conventional batch method.
In terms of making production more efficient, the group tried to improve connectivity and cut costs for equipment renewal by standardizing module structures, control systems, and electric systems as well as the piping that connects modules in order to facilitate process rearrangement. Further, for the analytical work that ensures the quality of each production process, it was possible to reduce manpower by developing and introducing explosion-proof automatic analytical devices with automatic sampling for quality-checking processes that previously required manual input. The next step is prototype production.
In addition to advancing the production and practical application of iFactory prototypes in this project, the aim is to display prototype modules, analytical devices, and control systems at the AIST Tsukuba Central Fifth Office, and to present the prototypes to those interested, centering on companies that will potentially use the product. In addition, "iFactory," a special-purpose company established in April 2019 with the aim of disseminating iFactory, will promote its growth in the developed production facility market.
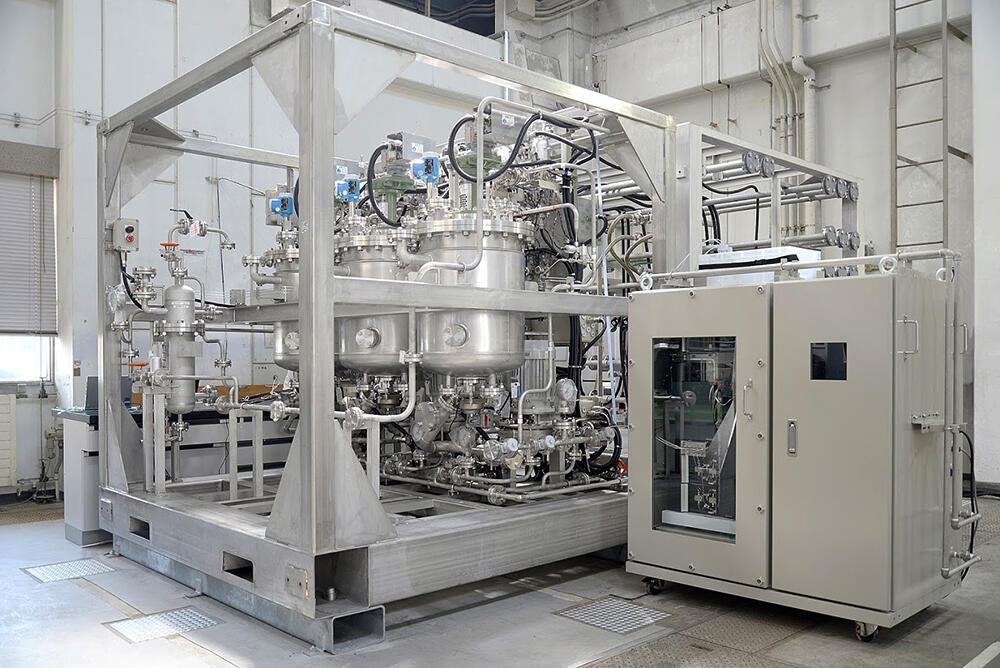
Credit: Yokogawa Solution Service Corporation
This article has been translated by JST with permission from The Science News Ltd.(https://sci-news.co.jp/). Unauthorized reproduction of the article and photographs is prohibited.