For the first time in the world, Japan Agency for Marine-Earth Science and Technology (JAMSTEC) Center for Mathematical Science and Advanced Technology Researcher Sayako Hirobe, Director Kenji Oguni, and others succeeded in almost completely reproducing the process of the instant fracture of chemically strengthened glass by the numerical analysis of dynamic fracture progress in a residual stress field. The developed dynamic fracture progress analysis method in the residual stress field can be used to formulate the rupture process of tempered glass and also of materials in extreme environments and can lead to the clarification of a new seismic generation mechanism owing to the residual stress field. Researcher Hirobe said, "This time, we carefully evaluated the process from the destruction of tempered glass to the results. However, it is expected to have various applications because it can reveal the universal physical phenomenon that governs the process in which the accumulated strain energy is released by fracture." This study was published in Physical Review Letters and Physical Review E.
Ordinary glass breaks with a slight impact, but chemically strengthened glass used in devices such as smartphones does not break easily. This is because high strength is achieved by generating strong compressive stress by ion exchange on the glass surface. However, the existence of compressive stress on the surface implies the accumulation of tensile strength inside. Therefore, when the chemically strengthened glass cracks inside, the accumulated force is released and it fractures immediately.
In the instant that chemically strengthened glass breaks, cracks grow fast inside the glass at a maximum speed of 2000 m/s. The release and reallocation of residual stress owing to crack growth interacts on a nanosecond time scale with the waves generated in the glass due to crack growth, and the cracks repeatedly branch and progress in unexpected directions. The analysis of the dynamic fracture progress process in such a complicated residual stress field has been difficult using conventional methods.
Through formulating the Hamiltonian value for the dynamic behavior of solid continuum with residual stress in the new particle discretization method using the particle discretization scheme finite element method (PDS-FEM) developed by Director Oguni, the research group analyzed the dynamic fracture progress process in a complicated residual stress field. The fracture behavior was observed in detail by inducing a constant impact to homogeneous glass with a width of 30 mm, height of 2 mm, and thickness of 0.7 mm, which was chemically tempered and made with different strength levels. Next, using the newly developed analysis method, numerical analysis was performed using a very fine mesh with a width of about 4000 divisions, height of about 260 divisions, and thickness of about 100 divisions; results showed that the cracks corresponding to the stress level generated in the experiment could be sufficiently reproduced. In addition to this, by visualizing the numerical analysis results with nanosecond time scale resolution, a detailed behavior of physical quantities that cannot be photographed in experiments was clarified. The distribution of residual stress inside the glass piece after the completion of fracture was also determined.
As a result of these developments, the research group succeeded in a numerical analysis that almost completely reproduces the process of dynamic fracture progress in a residual stress field for the first time in the world. "When we started, we were able to show that there was a fracture phenomenon whose end-state appearance was already decided," said Researcher Hirobe. This analysis method can reproduce the phenomenon that is universally observed in the process of releasing accumulated strain energy by fracture. Therefore, it can be applied to resolve various engineering issues wherein residual stress plays an important role, such as the fracture of metal welds, dessication cracks of various materials, and heat shrinkage cracks of concrete materials as well as for the evaluation of the soundness of structures that have undergone plastic deformation and damage to industrial products at high temperatures and high pressures.
These findings may also help to clarify how earthquakes occur. They may also lead to increased predictability of their occurrence. According to Director Oguni, "The current form of an earthquake is that strain builds up in and around the fault and is released, causing the earthquake to stop slipping where the fault is hard and slip is difficult. However, if the spatial distribution of strain accumulated at the beginning of an earthquake and the spatial distribution of energy required to destroy each point of the fault can be estimated, it may be possible to predict how an earthquake will occur by applying this analysis method. In the future, we would like to collaborate with groups conducting crustal structure exploration to predict the behavior of seismic faults at certain points."
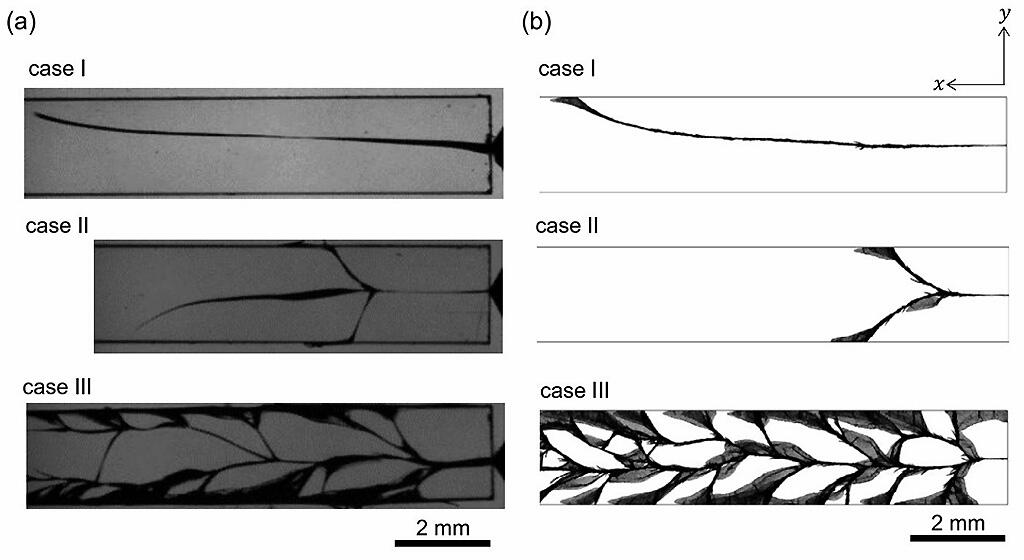
Credit: JAMSTEC
This article has been translated by JST with permission from The Science News Ltd.(https://sci-news.co.jp/). Unauthorized reproduction of the article and photographs is prohibited.