The Toshiba Corporate Research and Development Center Nano Materials and Frontier Research Laboratory announced on November 8 that they had developed a "sliding sheet-lattice matrix" for non-destructive ultrasonic testing for the maintenance and inspection of infrastructure, that can be attached to a probe (transmitter/receiver sensor), to provide both ultrasonic propagation and smooth operation. The developed sheet consists of a "soft sheet" and a "lattice material." Ultrasonic non-destructive testing can be conducted without wetting the inspection surface with a liquid contact medium. Toshiba is aiming for its practical application by the end of FY2024. Their results were presented at the 43rd Symposium on UltraSonic Electronics (USE2022) held in Kyoto, Japan.
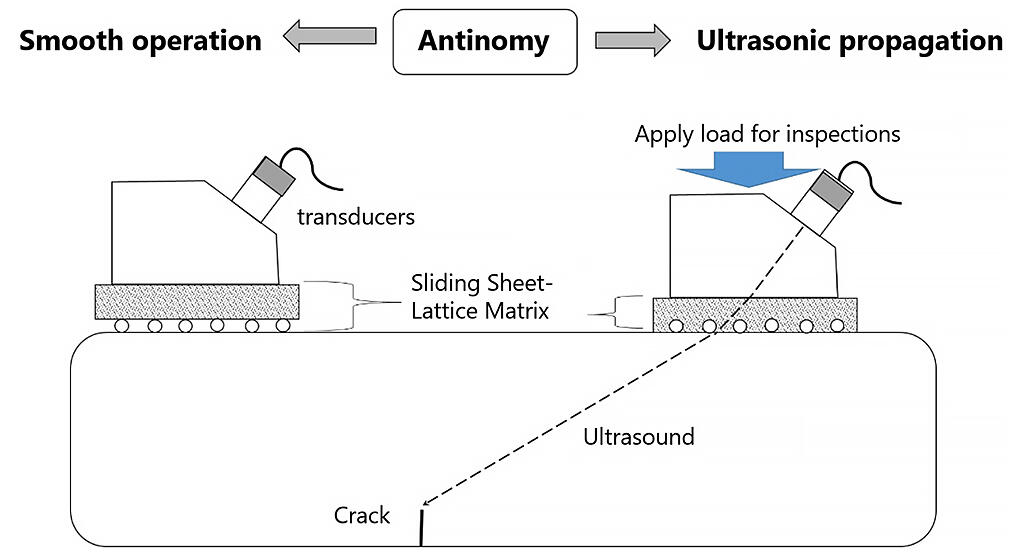
Provided by Toshiba
Ultrasonic non-destructive testing can detect material changes such as scratches inside an object being inspected without damaging it by transmitting ultrasonic pulses while moving the probe over the object and detecting the reflected waves. Since conventional testing uses the property of ultrasonic waves to reflect at the boundaries between different materials, the presence of air between the probe and the object being tested interferes with the inspection, requiring a liquid couplant similar to the gel used in ultrasonic examinations of humans to be applied.
However, the liquid couplant must be removed after inspection, and it cannot be used on some objects. Rubber was sometimes used as a couplant, but it had to be peeled off each time the probe was moved, which presented a problem of operability.
To address these challenges, Toshiba developed a "sliding sheet-lattice matrix" consisting of a "soft sheet" and a "lattice material." The "soft sheet" is a polymer (elastomer), and the "lattice material" is a lattice-shaped polymer, which can move smoothly over the object being inspected under normal conditions, and adheres to the object by applying a load when ultrasonic waves are transmitted and received. Since it can freely change shape and adhere to various objects for inspection, it can be used with a wide variety of inspection targets and probes.
When Toshiba used this sheet to inspect stainless steel, which is often used in infrastructure structures, the response time from the application of a load until ultrasonic waves sufficiently propagated to the inspected object and the reflected waves were measured was less than 50 ms, confirming higher responsiveness than conventional rubber sheets. The sheet responds rapidly, in approximately one-twentieth of a second, and can slide and move instantly when the load is stopped. Toshiba confirmed that about 10 measurements per second are possible. The durability of the product has also been verified to withstand 43,000 loads.
Since the sheet is attached to a probe, it can be mounted on an automatic inspection robot and is expected to improve the efficiency of maintenance and inspection. Moving forward, Toshiba will study the uses and applications for the sheet.
With aging infrastructures and human resource shortages around the world, the global market for non-destructive testing of infrastructures and other equipment is growing at an average annual rate of 4.7% and is expected to be a five trillion-yen market by 2028. At the same time, the non-destructive testing processes are being improved and made more efficient.
This article has been translated by JST with permission from The Science News Ltd.(https://sci-news.co.jp/). Unauthorized reproduction of the article and photographs is prohibited.