A research group led by Professor Shinjiro Umezu of the Faculty of Science and Engineering, Waseda University, and Professor Hirotaka Sato of Nanyang Technological University of Singapore announced on November 29 that they have successfully fabricated precision 3D metal-plastic structures with complex shapes by combining a newly developed optical 3D printer that can use multiple plastics and plating. On the significance of the achievement, the research group explained, "By combining metal materials and functional plastic materials, we can fabricate functional parts that cannot be created with a single material, and this will greatly promote the practical application and industrialization of 3D printing technology."
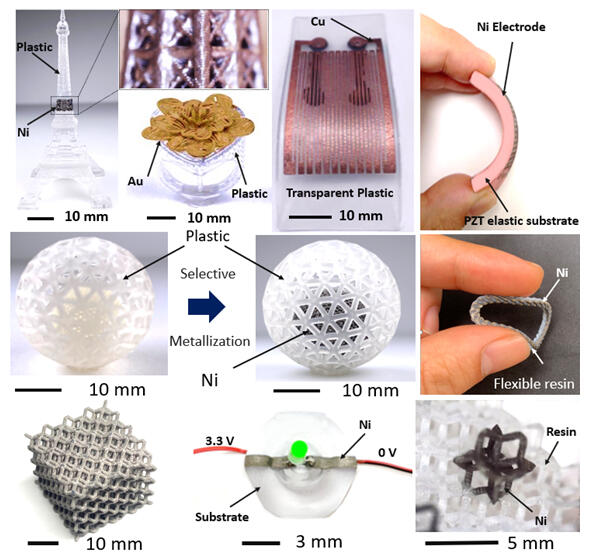
Provided by Waseda University
The research group fabricated a 3D structure combining a standard resin and a resin containing metal ions, and by applying selective electroless plating to the metal ion resin, they were able to provide clean metal plating on the plastic. This makes it possible to fabricate things such as various metal-plastic composite parts and electronic circuits with complex shapes at a resolution of 40 µm.
While it has been possible to fabricate high-precision plastic shapes on curved surfaces using optical 3D printers, it has not been possible to fabricate metal-plastic composite parts or electronic circuits in which metal is plated on internal surfaces in addition to 3D surfaces. Although plating can be applied to the entire surface of a plastic object created by 3D printing, the technology did not allow metal to be applied at arbitrary locations.
In their efforts, the research group developed an optical 3D printer that uses multiple resins, and can adjust the exposure time and other variables according to the resin that is used, to fabricate 3D structures combining standard and metal-ion resins (active precursor).
The current approach has several advantages, including the ability to produce complex metal-plastic 3D parts with specific metal patterns and the ability to build highly integrated and customizable 3D microelectronic devices.
The researchers fabricated a 3D object composed of plateable and normal resins with an optical 3D printer, and then plated the object so that the platable resin part becomes metal. The was based on a simple principle that allows complex electronic devices to be fabricated without the need for expensive manufacturing equipment or complicated processes.
Although it has been shown that 3D printers can create arbitrary shapes, the machines used to fabricate metal and plastic objects are different. This significant achievement demonstrates that a 3D printer can create complex 3D objects composed of metal and plastic by using plating.
This has shown that a variety of electronic devices can be fabricated independently and is anticipated to be highly effective in the development of robots and IoT devices, which need to be manufactured for next-generation electronics.
The research group is working with collaborators to create practical healthcare IoT devices and develop small autonomous robots with an eye on the future. The required functions and problems will change as where they are used changes, but the group will respond through discussions with collaborators. They are also working on improving the 3D printer to further enhance its performance.
Journal Information
Publication: ACS Applied Materials & Interfaces
Title: New Metal-Plastic Hybrid Additive Manufacturing for Precise Fabrication of Arbitrary Metal Patterns on External and Even Internal Surfaces of 3D Plastic Structures
DOI: 10.1021/acsami.2c10617
This article has been translated by JST with permission from The Science News Ltd. (https://sci-news.co.jp/). Unauthorized reproduction of the article and photographs is prohibited.