A research group led by Associate Professor Daisuke Suzuki of the School of Science and Technology at Shinshu University, in collaboration with the Yokohama Rubber Co., Ltd. (President and Chairman of the Board Masataka Yamaishi), announced the development of a high-performance polymer material that exhibits high resistance to cracking. This polymer material achieves high stretchability without the need for additives or organic solvents through the introduction of rotaxane molecules into specially designed polymer nanoparticles. The material can be easily fabricated by evaporating water from a dispersion composed solely of polymer nanoparticles and water. Furthermore, when immersed in a mixed solvent of water and ethanol, the material can return to its original nanoparticle state. High durability against cracks was confirmed through investigations into the properties of the film-like polymer material. This achievement is expected to contribute to the realization of a resource-circulating society. The research results were published in the June 16, 2023, issue of the academic journal Langmuir, published by the American Chemical Society.
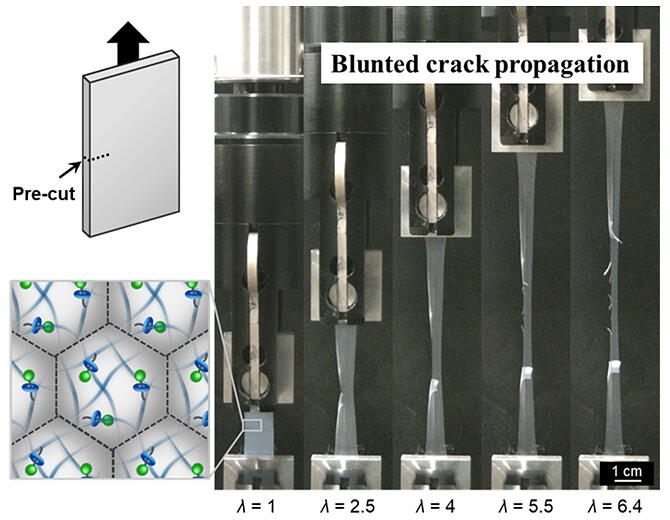
Provided by Shinshu University
The research group has been studying the control of the stability and decomposition of polymer materials such as plastics. In March of this year, they reported the successful formation of a high-performance polymer film via nanoparticulation of polymer chains (several tens of nanometers to 100 nm long) and their subsequent assembly. This approach allows simultaneous achievement of toughness and excellent decomposition.
The group confirmed that the formed polymer film can be repeatedly reused by simply immersing it in a solvent in which it decomposed back into the original nanoparticles. The current challenges in polymer recycling include using environmentally burdensome organic solvents and requiring higher energy than manufacturing processes.
Synthetic latex (a type of polymer rubber) formed fine particle films when a dispersion of polymer particles containing microparticles was dried. However, the challenge was the need for additives to prevent breakage at the adhesive interface between the microparticles.
The research group successfully fabricated fine particle films having high stretchability and resistance to crack propagation by introducing rotaxane molecules into polymer nanoparticles composed of polyacrylic acid ethyl—a material used in synthetic rubber—and methyl methacrylate (MMA), i.e., a representative plastic. Rotaxane molecules have a cyclic structure with an axel molecule threaded through them. It is known that gel materials crosslinked by the same molecules exhibit improved mechanical properties.
Fine particle films can be fabricated without requiring additives or other substances by simply evaporating the water from a nanoparticle dispersion solution containing polymer microspheres (approximately 100 nm in diameter). Furthermore, this fine particle film can be decomposed into the original polymer microspheres without degradation by immersing it in a mixed solvent of water and ethanol for approximately 24 h.
Fine particle films can be easily fabricated by linking polymer nanoparticles. This involves subjecting a solution of dissolved materials to ultrasound waves to form colloidal particles, synthesizing polymer microspheres within these particles using a mini-emulsion polymerization method, and evaporating water. A nanoparticle film was fabricated by adding just 0.02 mol% of rotaxane molecules to the nanoparticles.
In a peel test conducted to evaluate the durability, when a crack (incision) was introduced in a fine particle film, the film elongated to arrest the crack, and the crack propagated in a zigzag manner. In contrast, conventional films typically fracture without significant elongation as cracks propagate rapidly.
The research group investigated the internal structure of the nanoparticle film using techniques such as small-angle X-ray scattering. They observed that the polymer chains intertwine deeply with each other at the adhesive interfaces between the nanoparticles.
To investigate the cause of the crack propagation inhibition effect in the fabricated fine particulate film, they conducted experiments in which the peeling speed was varied (1−100 mm/s). They observed that the zigzag propagation of the crack diminished as the speed increased. This indicated the involvement of the mobility of cyclic rotaxane molecules in the phenomenon.
The group will extend their research to polymer materials with other properties and aims to develop materials that can be decomposed into polymer nanoparticles, recycled, and tailored for applications, e.g., involving light and temperature. Because polymers are also used in semiconductor bonding, replacing such materials is expected to facilitate the recovery of rare metals and other resources.
Suzuki stated, "Polymer recycling generally requires high energy and poses challenges in terms of degradation. However, I believe we have successfully overcome these limitations."
Journal Information
Publication: Langmuir
Title: Nanoparticle-Based Tough Polymers with Crack-Propagation Resistance
DOI: 10.1021/acs.langmuir.3c01226
This article has been translated by JST with permission from The Science News Ltd. (https://sci-news.co.jp/). Unauthorized reproduction of the article and photographs is prohibited.