Researchers at Yokohama National University revealed that a surface treatment method called "ball burnishing," in which a hard steel ball is pressed against a metal and rolled, can close and smooth out cracks on the surfaces of aluminum alloys (duralumin), increasing their fatigue strength and repairing them. This discovery is expected to extend the service life and improve the reliability of transportation equipment, which must be lightweight in nature. The proposed method has the advantage of shortening the polishing process during final finishing in parts manufacturing.
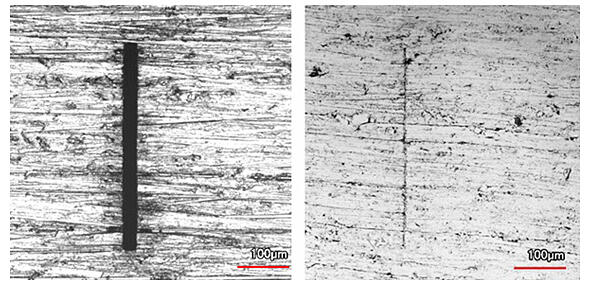
Provided by Prof. Koji Takahashi, Yokohama National University
When metals are subjected to repeated forces, microcracks develop on their surfaces and interiors. If left unchecked, these cracks will grow until the entire material breaks. Shot peening, in which the spherical particles of cast steel or glass are sprayed onto a material surface at high speed, is widely used to increase fatigue strength and hardness required to withstand repeated forces. However, this method has disadvantages such as reduced fatigue strength and poor appearance due to surface roughness caused by numerous particles hitting the material surface.
Professor Koji Takahashi of the Yokohama National University Graduate School of Engineering, who undertakes research into material strength, was consulted regarding the possibility of repairing scratches using ball burnishing, which uses the same principle of pressing a metal surface at points to increase fatigue strength, and research began in April 2022.
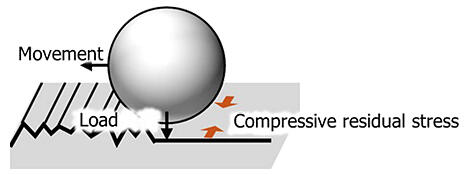
Provided by Prof. Koji Takahashi, Yokohama National University
Test pieces of duralumin were prepared for the present study. Slit-shaped scratches with a depth of 0.1 or 0.2 mm were made in the thinnest and weakest parts of the test pieces, and ball burnishing was performed by rolling a steel ball used in bearings back and forth around the scratch. Compared with a test piece that had not been ball burnished, the surface looked smoother, and roughness reduced by 80%.
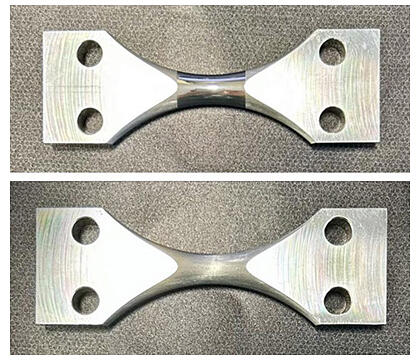
Provided by Prof. Koji Takahashi, Yokohama National University
When the fatigue strength of the test pieces was measured by bending it, the fatigue strength recovery was 22% without scratches, 143% with a scratch of 0.1-mm deep, and 216% with of 0.2-mm deep. In all cases, ball burnishing resulted in a higher fatigue strength than the unscratched test piece (without ball burnishing treatment).
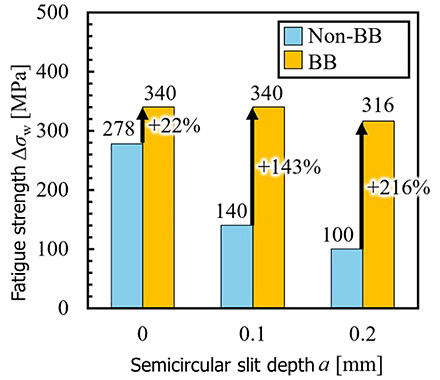
Provided by Prof. Koji Takahashi, Yokohama National University
According to Professor Takahashi, ball burnishing not only repairs scratches and increases fatigue strength but also smooths the surface simultaneously. By applying this technology at the final stage of the manufacturing of parts for bicycles, trains, aircraft, etc., it is possible to repair extremely small machining scratches that remain unnoticed during manufacturing. In addition, this treatment can be employed straightforwardly by attaching a special tool to an NC lathe, which is widely used in cutting and other processes, thereby simplifying the automation of the machining process.
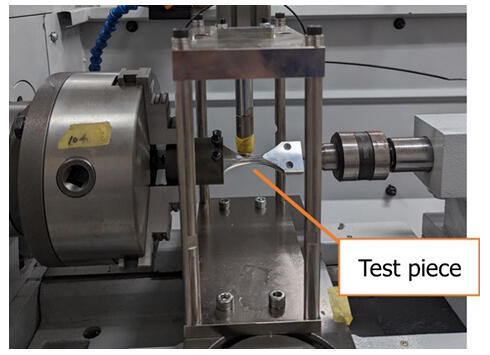
Provided by Prof. Koji Takahashi, Yokohama National University
In the future, the team plans to improve the method so that it can be applied to weak areas, such as welds, complex shapes, and other localized areas, as well as to verify the possibility of increasing the strength and repairing scratches in materials other than aluminum alloys.
The results were published in the international scientific journal Fatigue & Fracture of Engineering Materials & Structures and Yokohama National University also issued a press release.
Original article was provided by the Science Portal and has been translated by Science Japan.