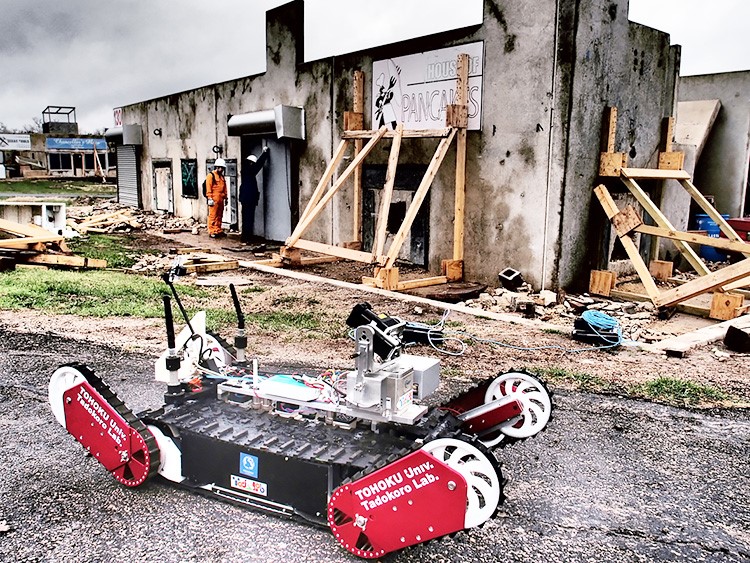
As Japan moves forward with efforts to build a disaster-resistant nation based on the Great East Japan Earthquake lessons, the use of robots in times of disaster has been attracting attention. Professor Satoshi Tadokoro of Tohoku University is a pioneer who has been leading the research and development of such robots in Japan. After his own experience in the Great Hanshin-Awaji Earthquake, he began developing robots that could "help people in need" in the event of a disaster. Having developed tough robots that can perform well at a disaster scene, what has he been thinking about, and what kind of future does he envision?
To "help people in need"
The origin of Tadokoro's robot development goes back to his childhood. At the time, animated films featuring robots such as "Astro Boy" were trendy. Growing up watching such anime, he majored in precision engineering and entered research and development, keeping his interest in robots.
Initially, Tadokoro was intensely interested in improving the efficiency and performance of robots as machines. However, his first turning point was at the Great Hanshin-Awaji Earthquake that occurred on January 17, 1995 and claimed the lives of approximately 6,500 people. While the damage was widespread, mainly in the Kinki region, Tadokoro witnessed the devastation as one victim in Kobe. A thought came to his mind, and memories of his childhood.
"Science and technology should be able to solve these problems, but the robots we have today are not able to 'help people in need.' On the contrary, no researchers even exist who try to achieve that. At this rate, we will not develop technology that can save human lives even in100 years. I don't know if we can do it or not, but we should start even from the grassroots."
We will develop robots that we can use in times of disaster to save as many lives as possible. That was the moment when "disaster relief" and "robots" came together in Tadokoro's mind.
Starting with listening to the victims
Tadokoro began his journey with great determination, but the road ahead was difficult. In the 1990s, most of the robots were so-called industrial robots engaged in assembling industrial products. So, many people wondered whether "robots that save human lives" could be the subject of research in the first place.
The first thing Tadokoro did was to interview the rescuers. Then, he conducted hearings and discussions with the victims as well as the firefighters and volunteers who rescued them. By doing so, he surveyed the actual situation of "how they rescued and how they got rescued. Then, he analyzed the results to extract ideas for what robots can support parts of rescue. For example, in the case of a rescue by diving into debris, he divided each task into "reaching the location of the person in need of rescue," "finding him/her," and "examining his/her condition" and then narrowed down which tasks can be handled by the robot.
In addition, he set up a study group in the academic society to identify issues regarding robots for disaster relief, involving other researchers in the process. The technology got better and better through the repeated discussions, the robot's mobility advanced, and they also realized the miniaturization of peripheral devices such as infrared cameras. This way, the disaster relief robot was taking shape that could withstand practical use little by little.
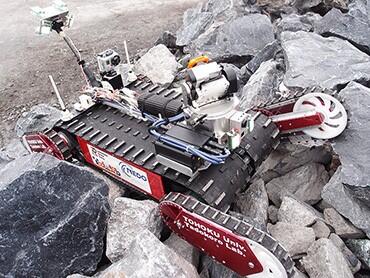
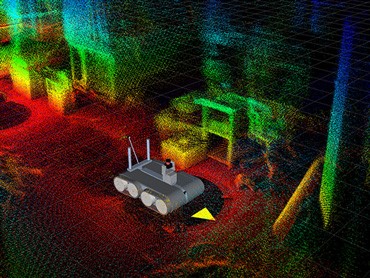
Quince's Contribution to Fukushima Nuclear Power Plant
Amid such efforts gaining social recognition, Japan was struck by another unprecedented disaster, the Great East Japan Earthquake. It is still fresh in our memories that earthquakes and tsunamis, and accidents triggered by them have caused tremendous damage. In response, Tadokoro and his research group deployed Quince, an emergency disaster response robot, in a search operation to investigate the inside of the Fukushima No. 1 nuclear power plant. As a result, it gained a detailed assessment of the damage and contributed to the later formulation of a work plan for the plant.
The development of Quince got greatly aided by an initiative that had been underway since before the Great East Japan Earthquake. That is "RoboCup," an international contest aiming to develop new technologies through competition robot development. Tadokoro had already launched the Rescue Division in 2001, which competes in the performance of robots at simulated disaster sites, as a new division of RoboCup. Tadokoro says that as the competitions went, "a system was created in which many researchers and students who came together without being paid, came up with ideas to solve various technical problems." Under such circumstances, the foundation of Quince, which combines high mobility with multiple crawlers and autonomous mapping in a closed space, was created in a bottom-up manner.
Tadokoro recalls his experience of the Great East Japan Earthquake, "It was the first large-scale disaster in human history where many robots were used in practice, tested, and achieved some success. On the other hand, first-deployed robots could not be used immediately in the field and often failed because it was for the first time. Due to the wide media coverage, the general public became more aware of the robots."
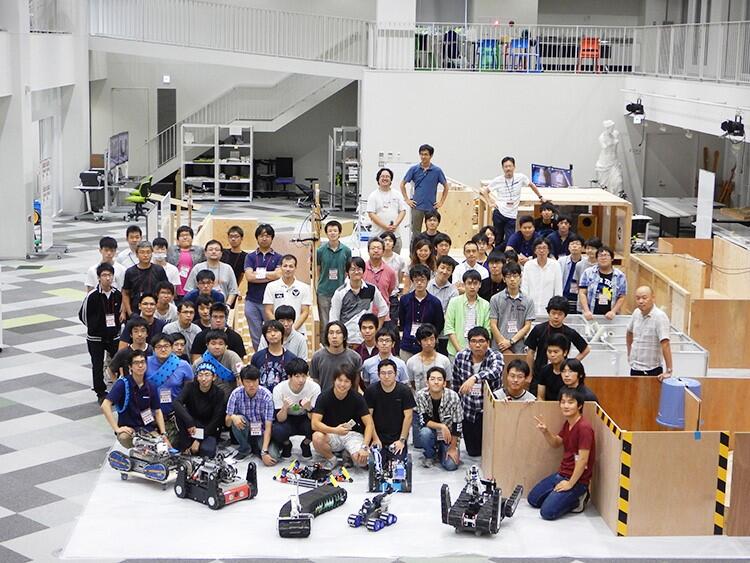
(Photo provided by International Rescue System Institute)
Coping with the harsh conditions is required in a disaster
The word "tough" often appears as a keyword in developing robots that Tadokoro is trying to reach. The term "tough" generally means "hard to break"or "tireless," but the concept of "tough" he is pursuing has a different meaning.
"For robots to be effective at disaster sites, they must be able to perform under a variety of harsh and adverse conditions. For example, it's useless if you could not do the job because the debris was too steep, or you could not see because it was too dark. Therefore, we must remove the constraints one by one so that the technology can work under severe conditions. This is the meaning behind the word "tough": ability to demonstrate the effectiveness of technology even under difficult site conditions," says Tadokoro.
Many unforeseen circumstances can occur in actual disaster relief situations like roads are bumpy or blocked with heavy objects. There are also many times when a robot's environmental awareness and autonomous intelligence do not work well. Tadokoro stresses that disaster rescue robots are required to have the ability to overcome them, find the person in need of rescue, and carry out rescue operations: in a word, capable of functioning under the severe conditions required at disaster sites.
Closing the gap with user needs
Nevertheless, realizing functions and performance under the problematic conditions demanded by users is beyond current science and technology limits. It is impossible to realize the production of an all-purpose robot. There is a trade-off between the usage conditions and functions or performance.
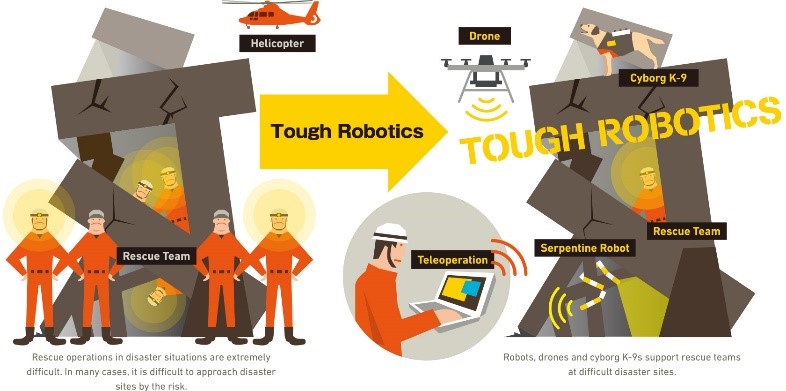
(Source: https://www.jst.go.jp/impact/en/program/07.html)
Tadokoro says it is essential to determine what is required, based on how the equipment is used in practice, to develop "tough" robots. "In a situation where the capacity is limited, it is necessary to sift through the functions and create the best system for the purpose. To do so, we need to fill the gap between the user side and the researcher side working on the development." In the beginning, the actual robot users and the developers do not agree on what they are wanting. The goal is not to create technology but to create a tool that can effectively deal with disasters. Therefore, the development of disaster relief robots requires creating a forum that connects and allows the two parties to exchange opinions and understand the respective positions.
"To be able to cope with the harsh conditions required in a disaster" and "to close the gap with user needs." These two points, according to Tadokoro, are issues that have been addressed over the past ten years, from the Great East Japan Earthquake to the current spread of the new coronavirus infection.
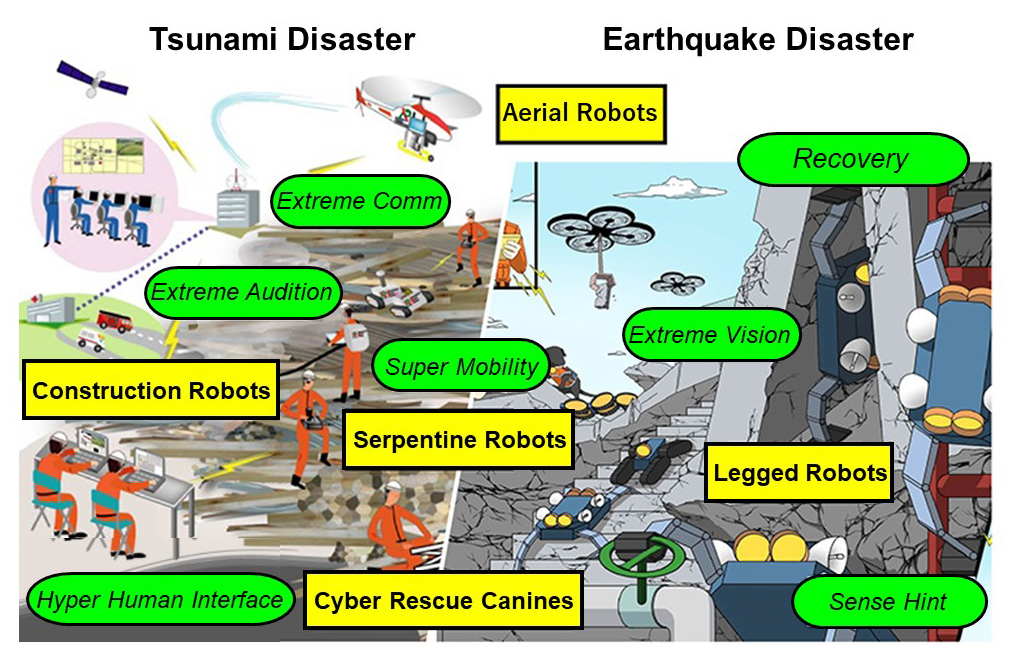
Using the technology of disaster relief robots in times of peace
"Most of the damage caused by the Great East Japan Earthquake, which people had called 'unexpected,' was predictable. It's the same with infectious diseases. It had been predicted for a long time that a pandemic (global outbreak) would one day occur, and in fact, SARS (Severe Acute Respiratory Syndrome) spread. We could have prepared for it if we had wanted to. However, I think there is still an aspect where the necessity of such preparations has not been seriously considered, and a decision has not been made as to whether we should prepare for it or not," says Tadokoro.
The importance of creating a social infrastructure based on the premise that disasters will occur and a system to support it is no different for disaster relief robots. Tadokoro believes that "only science and technology have the power to solve this problem. " He proposes to build an "ecosystem"focusing on disaster relief robots as a peacetime precaution. One way to do this is to actively utilize the technology developed for disaster relief robots in the ones that we use during ordinary times. Using technologies created for disasters in peaceful times, we must promote technological development and lower the barriers to social implementation.
It is necessary to change all researchers, companies, and public organizations involved in development to achieve this. There is a need to promote research & development to solve social issues and expand support systems for young researchers to take on the challenge of developing new technologies. However, Tadokoro says that the most important thing is "raising the public's awareness, the biggest end-user."
Like an infectious disease, you never know when a large-scale disaster will strike. In other words, everyone who lives today can be a party to it. Therefore, rather than leaving research & development to a specific person, everyone should think about using the technology, which is the kind of "preparedness" we need to face our shared challenge of disasters. I believe that such preparedness is also essential to counter the threat of the new coronavirus that we are now facing.

Satoshi Tadokoro
Professor, Graduate School of Information Sciences, Tohoku University.
He received his master's degree from the University of Tokyo in 1984 and became an assistant at the Faculty of Engineering, Kobe University, in 1986. After working as an assistant professor at the same university, he assumed his current position in 2005. From 2014 to 2018, he was ImPACT (Program for the Promotion of Innovative Research and Development) Program Manager for "Tough Robotics Challenge." He has received several awards, including the Commendation for Science and Technology by the MEXT minister. He specializes in the research & development of robots and ICT for supporting emergency response, recovery, and prevention of disasters, based on manufacturing technology. He is an IEEE Fellow and a Ph.D. in Engineering.
Original article was provided by the Science Portal and has been translated by Science Japan.