Plastics do not easily decompose in nature owing to their high stability and durability. In an effort to tackle this problem, Dr. Yoshiharu Doi, Researcher Emeritus at RIKEN, has succeeded in putting "biodegradable plastics" using microorganisms into practical use. Currently, 5000 tons of this plastic are being produced per year and it is being used both in Japan and Europe. This research has been taken up by Hideki Abe, Team Leader, and Tomohiro Hiraishi, Senior Research Scientist, RIKEN Center for Sustainable Resource Science. The research team will clarify the biodegradation mechanisms of these plastics in natural environments. Furthermore, they will take on the challenge of developing new materials that, while maintaining durability, can also decompose in the various environments when discarded.
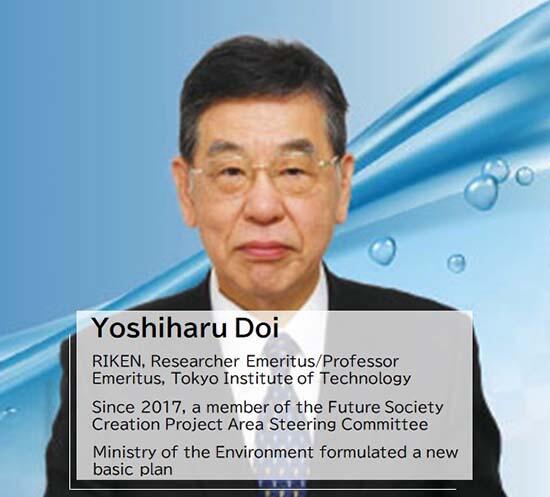
Changing entry and exit points of the plastic cycle
In Japan, approximately 10 million tons of plastic are manufactured annually. Plastics are widely used, and most are derived from fossil fuels. This large consumption of fossil fuels has caused the atmospheric concentration of carbon dioxide (CO2) to gradually increase, and there is concern regarding the impact of these practices on the global environment. Plastics released into the environment persist in the oceans and rivers without being degraded and have long-term impacts on ecosystems.
Recently, so-called bioplastics have gained increasing attention as a possible solution to these issues. Bioplastics is a general term for "biomass plastics" made from biomass such as plants and "biodegradable plastics" that can be decomposed by microorganisms (Fig. 1). The development of "biomass plastic" focuses on the raw materials used to make plastics, i.e., emphasis is on the cycle entry point, whereas the development of "biodegradable plastic" focuses on changing the biodegradability of the plastic substances, i.e., emphasis is on the cycle exit point. Biomass plastics are not always biodegradable, and biodegradable plastics may also contain fossil fuel-derived plastics. In this manner, problems related to plastic cannot be solved without changing the "entry" and "exit" processes. In response to this issue, the government will support the conversion to bioplastics.
In 2019, the Ministry of the Environment formulated the "Fourth Basic Plan for the Promotion of a Sustainable Society." The plan aims to produce approximately 2 million tons of biomass plastics in Japan by 2030, which is 20% of the current annual production of plastics.
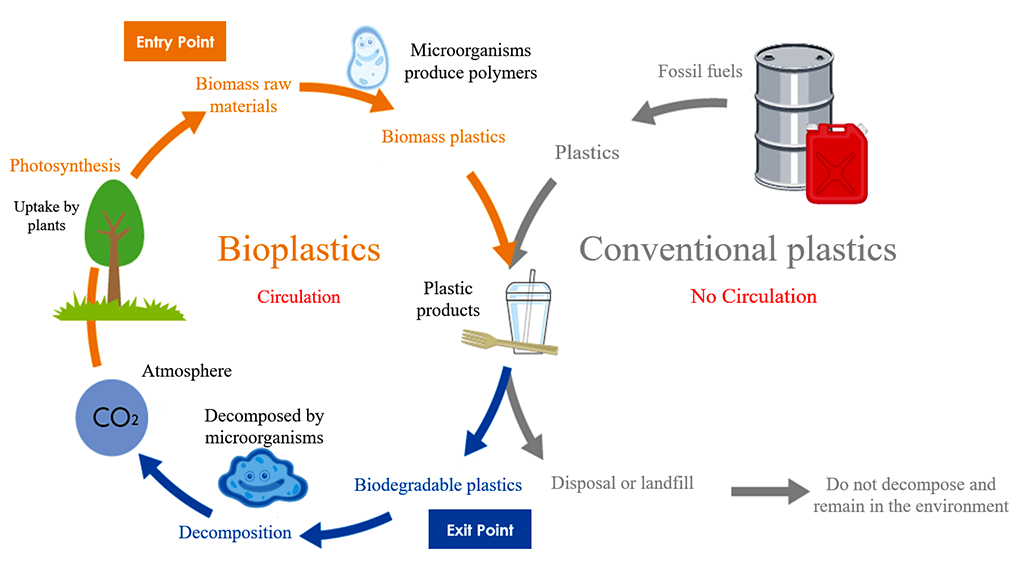
A "forgotten" polymer
The discovery of microorganisms that make plastic
The demand for biodegradable plastics is expected to increase in the future and one pioneer in the field is Yoshiharu Doi, a Researcher Emeritus at RIKEN. When he assumed the post of Assistant Professor at the then Department of Chemical and Environmental Engineering, Tokyo Institute of Technology, in 1984, plastic garbage had already become a major social problem around the world. He wanted to apply polymer research to environmental issues and set plastic recycling as his research theme.
One of his hobbies was fishing and Dr. Doi was worried that plastic fishing lines, which do not decompose in nature, are harmful to marine life. When he began researching plastic recycling, he was shocked to learn that there are microorganisms in nature that synthesize polyester, which is a chemical fiber, within their body. "My area of study is chemical synthesis. I thought that it might be possible to develop a biomass plastic that connects both the entry and exit points of the plastic use cycle into the biomass cycle; a plastic that is both biodegradable and can be biosynthesized by microorganisms from biomass-derived raw materials," said Dr. Doi. As a result of this find, Dr. Doi changed the course of his research in the direction of biodegradable plastics.
While reviewing past literature, Dr. Doi discovered a stereoregular polymer called PHA (polyhydroxyalkanoate) (Fig. 2). PHA is a "forgotten" polymer that, in the 1920s, was known to be produced by microorganisms. Dr. Doi used this fact as a clue to begin his quest, and in 1987, he discovered microorganisms that synthesize everything from hard plastic to soft rubber. "Our research was eventually highlighted in newspapers. Before that, no one paid much attention, and barely anyone attended our conference presentations," says Doi, reminiscing on those days.
Twenty-five years of joint research
Successful mass production of PHBH
In 1989, Dr. Doi began collaborating with Kaneka, a chemical manufacturer, for his research. They aimed to create high-performance PHA using vegetable oil, which has higher productivity than sugar, as a raw material. First, they searched for new microorganisms that synthesize PHA from the soil around Kaneka's vegetable oil plant. "I speculated that if Kaneka has a food-related division that handles vegetable oil, margarine, fish oil and similar products, there may be microorganisms nearby that can use vegetable oil as raw materials," predicted Dr. Doi. He was right. In 1991, Kaneka discovered a new type of microorganism that produces PHBH (3-hydroxybutyrate-co-3-hydroxyhexanoate copolymer) (Fig. 3).
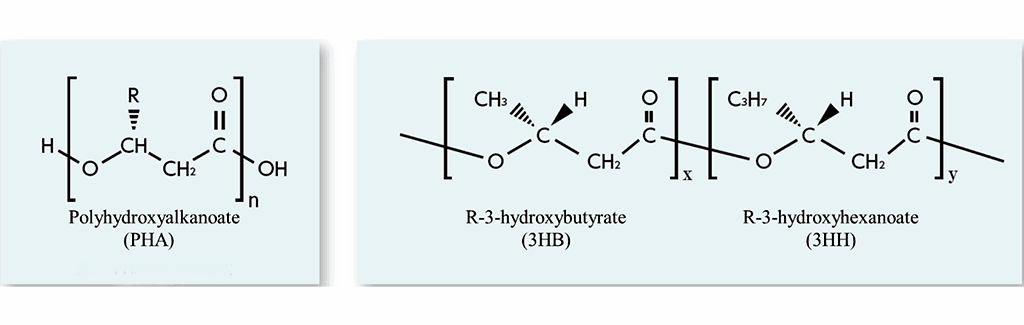
Fig. 3 (right) Chemical structural formula of 3-hydroxybutyrate-co-3-hydroxyhexanoate copolymer (PHBH)
The crystallinity of PHBH can be adjusted by changing its BH composition. Hopes were high because it was found that PHBH was easy to mold and was quite durable, making it suitable for plastics. However, there were also challenges. "Microorganisms synthesize polymers and store them in their bodies, similar to how we store fat subcutaneously. However, this means that the upper limit of production is approximately 30% of the weight of the cells. This was inefficient and impractical. I did not think we would be able to implement this technology," says Dr. Doi.
In 1996, after transferring to RIKEN, Dr. Doi succeeded in creating organisms that accumulate up to nearly 90% of their body weight in PHBH using genetic modification techniques (Fig. 4). This was a breakthrough, and joint research with Kaneka which had been suspended, promptly resumed.
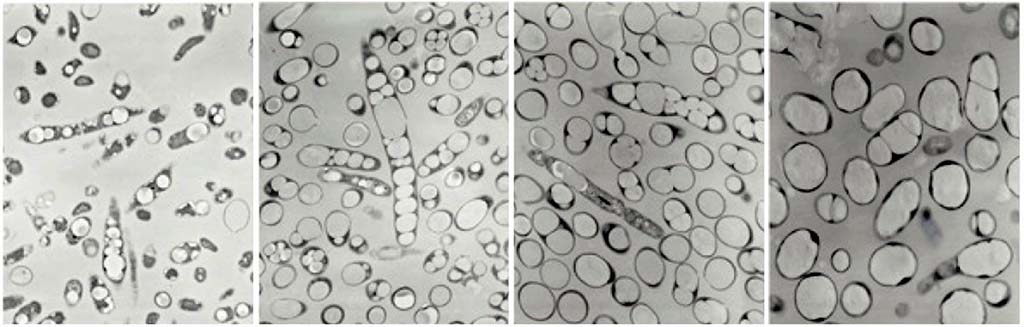
(Images provided by Kaneka)
In 2009, using a development project commissioned by the Japan Science and Technology Agency (JST), Dr. Doi and his team conducted a production demonstration experiment in which microorganisms were cultivated in a huge culture tank 100,000 times larger than the previous laboratory experiments. By combining the power of chemistry with polymer technology and the power of biotechnology with fermentation technology, Dr. Doi and his team established a process for separating and purifying PHBH from the microorganisms that produce it. The annual production of PHBH was 1000 tons in 2011, and the process was put into practical use in 2014 (Fig. 5). "The joint research project took 25 years. Although we encountered many difficulties in reaching this point, I would like to express my deepest respect for the people of Kaneka who persevered to the end. Currently, we are expanding the annual production to 5,000 tons, and within a few years we aim to produce 20,000 tons per year, and finally 100,000 tons per year," says Dr. Doi. He looks forward to future developments.
The PHBH produced by Dr. Doi and Kaneka can be biologically synthesized by microorganisms from biomass-derived raw materials. As a biomass plastic which is also biodegradable, it addresses both "entry" and "exit" into the bioplastic cycle and is being used overseas. In recognition of these achievements, in 2019, he received the 3rd Bioindustry Award sponsored by the Japan Bioindustry Association. In the future, there will be many opportunities to obtain products made from PHBH in Japan as well.
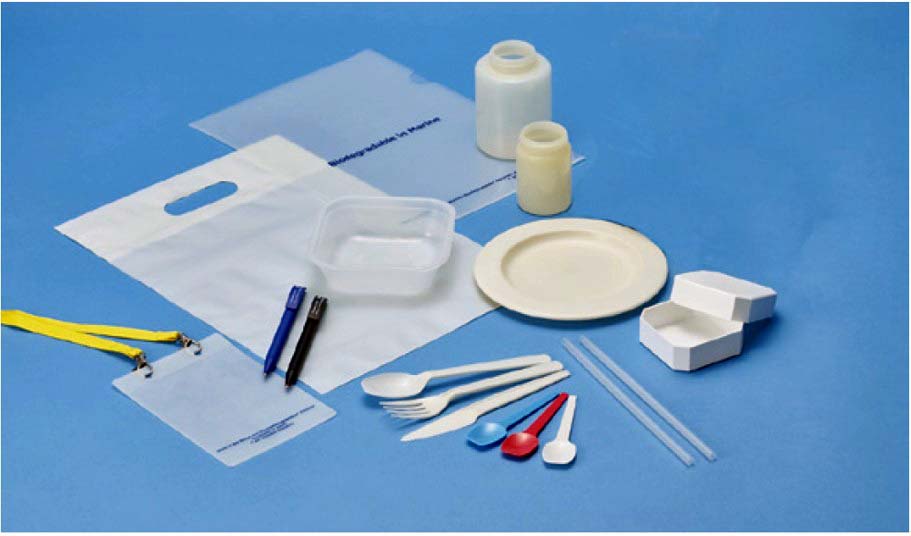
(Images provided by Kaneka)
Degradation performance that varies depending on the environment
Building a new circulation system
Currently, Dr. Doi 's research is being followed up on by a bioplastic research team led by Hideki Abe, the team leader at the RIKEN Center for Sustainable Resource Science. Dr. Abe and his colleagues are working on the synthesis of new functional biomass polymers from plant biomass using chemical and biological techniques. One of their research projects has been to take on the challenge of developing biodegradable plastic suitable for diverse environments. This effort is helmed by team member Tomohiro Hiraishi, a Senior Research Scientist. By making plastics that can be degraded as intended in various environments, they intend to build a new circulation system centered on biodegradable plastics.
Biodegradable plastics are eventually completely broken down into CO2 by microbes, thereby returning resources to nature. CO2 is taken up by plants via photosynthesis. Subsequently, when these plants are used to generate biomass plastics, a cycle is formed. To form this cycle, it is first necessary to clarify how plastics are biodegraded in various environments. Even if a particular plastic is "highly biodegradable," the degree of degradability varies considerably depending on the environment and the type of plastic. At present, there are only a few plastics such as PHBH that show high biodegradability in seawater (Fig. 6). "Biodegradable plastics are broken down by enzymes secreted by microorganisms that exist in the natural environment such as soil, rivers, and the sea. If we can clarify the mechanism by which different plastics are biodegraded in each environment, we can design plastics with biodegradability suitable for each particular environment," says Dr. Hiraishi.
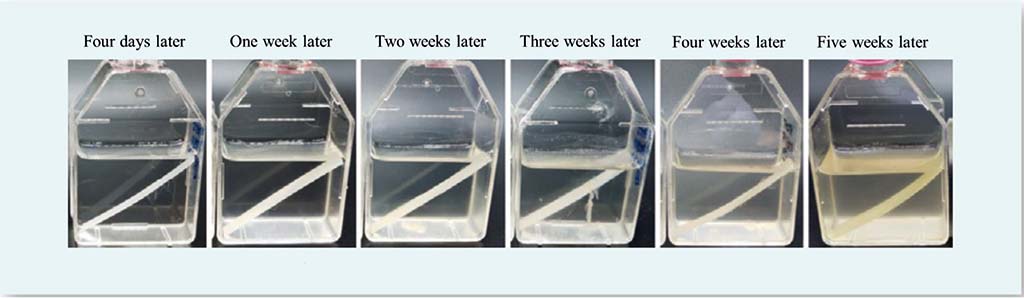
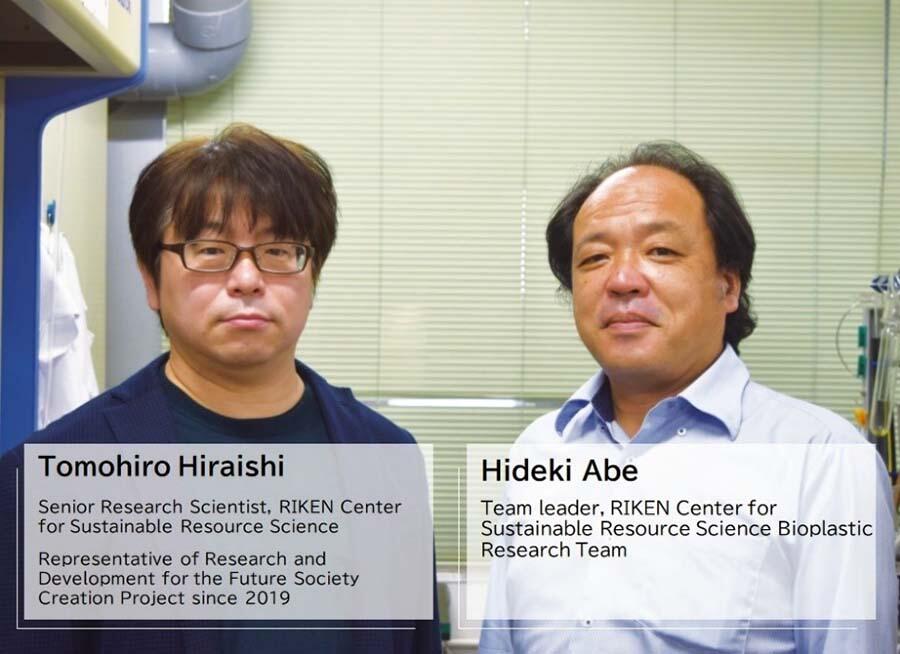
Focusing on enzymatic reactions
Clarifying the mechanism
Conventionally, the oxygen consumption (biological oxygen demand, BOD) during microbial degradation of plastic is measured, and the structural analysis of residual plastic is conducted using nuclear magnetic resonance equipment. These methods do not allow direct observation of the actual degradation of plastic by microorganisms or enzymes. Dr. Abe and Dr. Hiraishi, who believed that plastic-degrading enzymes hold the key to biodegradability, focused on the chemical reaction between plastics and plastic-degrading enzymes. "As a result, the reaction mechanisms between plastic and plastic-degrading enzymes have been gradually clarified," Dr. Abe said. Based on such research results, various biodegradable plastics have been chemically synthesized or biosynthesized, and their biodegradability has been evaluated. Consequently, it has become clear that biodegradability differs greatly between different types of plastics depending on the environment. Furthermore, it was also found that even with the same plastic, the decomposition performance by enzymes and the decomposition performance in the natural environment are not always similar.
The expected process of plastic biodegradation is divided into six stages (Fig. 7). First, microorganisms adhere to the surface of the plastic. Enzymes secreted by the microorganisms then degrade the plastic. Following this, Microorganisms grow using the degraded product as a nutrient source to produce colonies. Bacteria that do not decompose plastic also adhere to the product, forming larger colonies and forming a biofilm that covers the colonies. Dr. Hiraishi emphasizes that focusing on the reaction mechanisms between plastic and plastic-degrading enzymes alone is not enough. "We need to analyze in detail what triggers biodegradation in the actual natural environment."
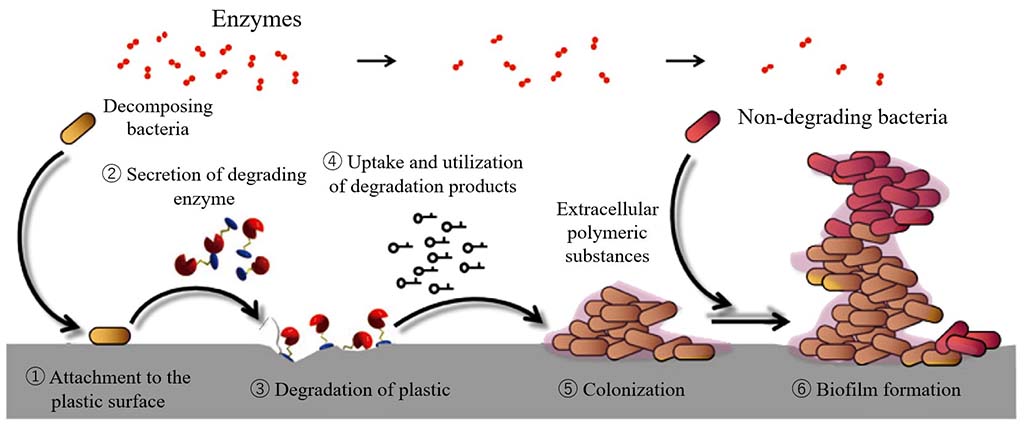
Establishment of real-time analysis method
Development of materials suitable for fishing equipment
Therefore, they began to work on the development of a method for observing biodegradation processes in real time in the same state as the natural environment, instead of analyzing it individually as was done in the past. By introducing new methodologies, such as omics analyses that comprehensively investigate the types of microorganisms that decompose specific substrates with particular enzymes, and isotope labeling methods that measure how metabolites are used by microorganisms, they have been able to achieve real-time measurements of all processes. "If we can clarify the mechanism of biodegradation in the natural environment with this measurement method, we will be able to evaluate biodegradability more appropriately. I would like to make use of this information in the design of plastics," says Dr. Hiraishi emphatically.
At present, Dr. Abe and colleagues are developing biodegradable plastic with stability and biodegradability for fishing threads and fishing nets, products which are among the major contributors to marine pollution. "These materials must have high durability during use, but also comprise materials that biodegrade quickly after a certain amount of time or once their environment changes. At the same time, increasing the biodegradability reduces the stability of a material. It is a trade-off relationship," says Dr. Abe, explaining the difficulty of product development. Studies are also under way to create biodegradable plastics with some switching function, for example, biodegradation begins only when salinity, temperature, pressure, or acidity change.
Approximately 40 years have passed since the study on biodegradable plastics began. The research project that has been handed down from Dr. Doi to Dr. Abe and Dr. Hiraishi is now about to expand alongside world trends. Both fundamental and applied research that has been underway for many years will continue to generate a variety of cyclic biodegradable plastics. These three researchers will continue to make steady strides toward the realization of a low-carbon society.