Based on the preliminary figures of the October 2020 census, the population of Akita Prefecture is declining by approximately 14,000 people each year, which includes 3000 young people. This trend, if not suppressed, will likely affect future social activities. Here, the research activities being conducted to contribute toward improvements local communities are described.
The words of my mentor, who supported my research
During orientation at my university, my mentor told me, "The essence of engineering is to connect heaven and earth." Ever since, I have kept these words in mind: industries must benefit the people.
Acquisition of the seeds of innovation through meeting people
In 1994, I switched jobs by quitting my company and joined the Akita Industrial Technology Center; this was a major turning point in my research. Through my previous connections, formed via technical consultations with companies in the prefecture, I met Professor Toyohisa Fujita of Akita University (currently Professor Emeritus of the University of Tokyo) and asked him to be my mentor. At the time, he was researching electrorheological fluids that respond to electric fields and exhibit a thickening effect, as well as their applications. I attempted to examine the mechanism via which this thickening effect occurs. To this end, dielectric silicone oil was employed as a solvent, and artificial diamond particles with high hardness were prepared using semiconductors as the dispersed particles. Subsequently, an observation experiment was conducted to deduce this mechanism. When evaluating an electrorheological fluid, a DC electric field or a 50 Hz AC electric field is generally applied to evaluate the thickening effect. Therefore, in the aforementioned observation experiment, parallel electrodes were installed under a microscope, and an extremely low-frequency electric field was applied after dropping the adjusted liquid. Immediately, as shown in Fig. 1, the diamond particles exhibited an active behavior in the liquid. I still vividly remember how surprised I was on observing this phenomenon.
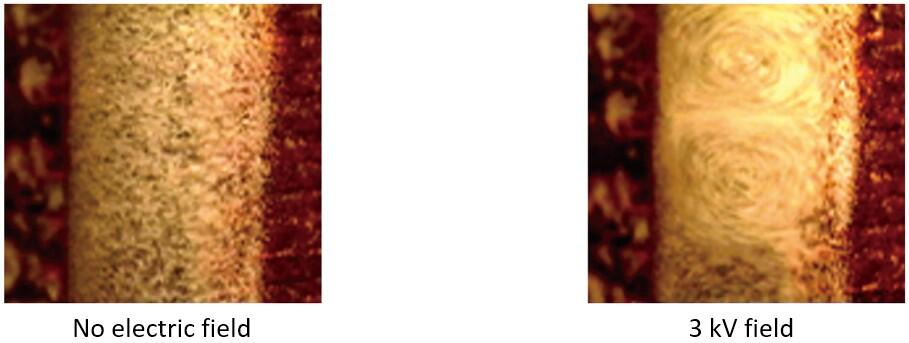
In an attempt to establish a startup based on this phenomenon, I referenced the relevant literature and asked my professors for guidance. This led to further encounters with people. This behavior was named as electric field abrasive grain control technology, because it can be used to control the placement of abrasive grains in a fluid medium. I subsequently applied for a patent. After presenting this phenomenon to the president of a small-diameter ball end mill manufacturer in the prefecture, we commenced joint research, expecting that this phenomenon could potentially be used to extend the life of small-diameter tools, which was an unsolved problem at the time.
First, the causes of shortened tool life were investigated; it was presumed that the convex burrs remaining after the machining of the cutting edge resulted in reduced tool life. To remove such burrs, the cutting edge of a high-hardness cBN ball end mill was used as an electrode; a rotary surface plate was set below to serve as the other electrode. When a diamond-dispersed fluid was dropped onto the pad and contact-rotated, under the application of a low-frequency AC electric field, the abrasive grains gathered at the cutting edge. Typically, polishing is time consuming owing to the scattering of the abrasive grains; however, this polishing method could serve as a technique whereby the abrasive grains are collected by the action of an electric field. Thus, the convex portion of the blade can be finished within a shorter time. In addition, to evaluate the improvement in the tool life, the tools made using this method were investigated. The point at which the cutter mark generated by machining was disturbed was considered to be a marker of the end-of-life of that tool. Using this metric, we determined that tool life was nearly doubled. By introducing this approach in the market, it has now become possible to directly process steel with a hardness which was impossible thus far. This approach was suggested as a new energy-saving machining method to replace electric discharge machining technology, which is time consuming, and also accepted as a proposal to improve the production efficiency for customers.
Based on this result, we applied for the competitive funds provided by the Ministry of Economy, Trade, and Industry in order to create new tools. Thus, the transformation from a subcontractor to a manufacturer, which the president dreamed of, was realized. In this manner, we were able to obtain new seeds of innovation and solve corporate issues, improve corporate values, and finally transform into a research and development (R&D)-type company and expand management. With this achievement, we received the "Minister of Education, Culture, Sports, Science and Technology Award" together with our collaborators in 2018, and we were able to pass the business on.
Collaboration between the medical and industrial sectors by matching seeds and needs through encounters with people
How can we encourage young people to stay in the prefecture? How can we encourage those who have left the prefecture to return to Akita? Considering these issues from the perspective of a researcher and in light of the aforementioned research, where a subcontracting company was transformed into a R&D-type corporation, I believed that there might exist an approach to create "admired companies."
During this period, I met various teachers from the Japan Society for Precision Engineering. In 2003, we established the "North Tohoku Nano Medical Cluster Study Group" (First Chairman: Former President of Iwate University, Dr. Akira Iwabuchi; Current Chairman Dr. Hiroshi Nanjo, Division of Clinical Pathology, Akita University Hospital) to showcase the research results of the latest precision processing technology to the companies in this area and offer them a chance to notice the findings of researchers in the area. The catchphrase of this association was "Innovation is accelerated when people meet one another." At the meeting, it was suggested that "the future of precision engineering is medical equipment." Our R&D-type study group, which aims to contribute toward solutions for social issues, assembled three times a year, prior to the pandemic. Through this study group, enterprises in northeastern Japan have worked together to put forth ideas and obtain competitive funding from the national government.
The electric field slurry polishing technology was created as a water-based slurry control method based on the electric field abrasive grain control technology. Technologies for improving productivity and saving slurry resources have been developed for the optical parts industry in Akita Prefecture. In this research, it was found that a three-dimensional active stirring action can be obtained by applying a non-contact electric field to microliter microdroplets, as shown in Fig. 2. It is known that microliter droplets are dominated by surface tension, and it is difficult to cause mixing within them.
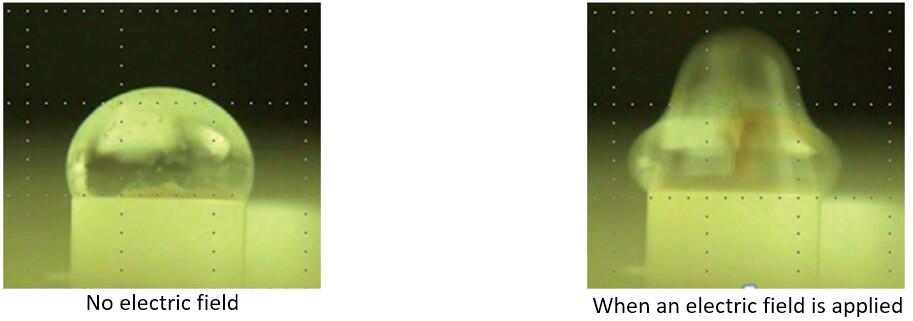
To observe the behavior of dispersed particles in a droplet, an electric field of 3 kV was applied externally to a 100 μL droplet prepared by adjusting calcium carbonate particles of approximately several micrometers. It was found that the particle movement speed could be increased by 1,200-fold. It was also clarified that the movement speed is improved by 10-20 times in a biological sample. Another notable feature of this stirring technique is that the liquid temperature does not increase during stirring. However, the ultrasonic agitation technique suffers from a problem in that accurate information cannot be obtained; this is because the apparent concentration increases due to the deformation of tissues and the evaporation of droplets, caused by the increase in the liquid temperature. This technique was termed as electric field stirring technology. I first introduced this research to Professor Yoshihiro Minamiya of Akita University Graduate School of Medicine (currently the director of the Akita University Hospital), who invited us to deliver the keynote speech at this group's September 2011 meeting. I informed him how this technology could help accelerate hybridization, which is used in DNA testing, by a factor of 5. This became the starting point of our joint work together. Dr. Minamiya subsequently informed me that he and other researchers were struggling with a particular problem, i.e., "immunohistochemical staining," a useful pathological diagnosis method that often requires a long time to produce diagnosis results. Is it possible to obtain diagnostic results during surgeries by applying electric field agitation technology? Can this be achieved within 30 min? These were his questions. Joint research was commenced immediately, i.e., in the following week.
The immunohistochemical staining method involves a two-step antigen-antibody reaction step. Previously, this step required 120 min, and a total of 150 min was required obtain the diagnostic results. In the meantime, however, the patient's surgery cannot be halted. Hence, the diagnoses are generally dependent on the traditional HE staining method and confirmed postoperatively using the immunohistochemical staining method. If the immunohistochemical staining results are obtained during surgery, the surgeon can select the optimal treatment policy based on highly accurate diagnosis results. Previously, if the diagnosis results from the HE staining method during the operation and those form the immunohistochemical staining method after the operation differed, the operation was repeated; this places a significant burden on the patient. Therefore, if the diagnosis results of immunohistochemical staining can obtained during the operation, the burden on the patient and the medical costs can be reduced. The results of the joint research indicated that clear results can be obtained within 20 min. Thus, it is possible to inform the surgeon of the diagnosis results within 30 min; this includes the time needed for the pathologist to form a diagnosis. Immediately, we approached manufacturing companies in the prefecture through the study group and proceeded with the development of a prototype by leveraging their strengths. This constituted the start of the Akita-launched open innovation through medical-engineering collaboration.
To spread this technology among the medical community, the "Rapid Immunology Study Group" was setup with the participation of pathologists from 7 universities and 1 hospital. This aimed at improving skills related to wide-area, detailed evaluations and advanced dyeability. A medical device manufacturer also joined us to comply with the Act on Securing Quality, Effectiveness, and Safety of Pharmaceuticals and Medical Devices (Pharmaceutical Machinery Law). The "rapid immunodiagnosis device," shown in Fig. 3, was launched in 2014. It has already been reported that this device is being used to support the diagnoses of more than 1,000 patients. This was a valuable experience associated with creating manufacturing that is beneficial for people.
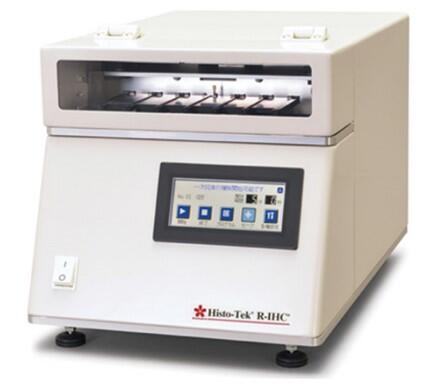
Several patents related to this device have been registered and received the Commissioner of the Patent Office Award in 2019 and the Minister of Economy, Trade and Industry Award of the 8th Japan Manufacturing Awards in 2020. Currently, at the request of the pathology department, further developments to convert the manual device to an automated device are steadily underway; this product is scheduled to be launched in 2022. Through such medical-engineering collaboration that incorporates industry, academia, and government, truly "altruistic" research and development can be achieved in Akita. In the future, we plan to focus on innovations in telepathology diagnoses through digital transformation (DX) and other means. We hope that this will lead to the"building of a safe and secure medical system in the region" and serve as an opportunity for people from the central region to move to Akita Prefecture.
An approach for promoting "admired companies" that work to combat population decline
Such study group activities and joint research indicate that young people can contribute toward the promotion of altruistic R&D-type companies that remain in the local area. Based on my previous joint research, approximately 10 companies have transformed into R&D-type companies. Nevertheless, certain companies have also succeeded in terms of business. In the future, we plan to continue explaining the importance of "joint research to develop and enhance innovation seeds," an approach that can help transform a smaller company into an R&D-type company. Furthermore, applying and subsequently being selected for large-scale competitive funding, will improve corporate recognition and corporate values; this will also provide young people with an opportunity to learn about the existence of R&D-type companies. Our new project aims at "the realization of an altruistic and admired company" by addressing social issues. I hope that the essence of such research activities will be passed on to the next generation. By continuing our efforts to contribute toward "solutions" that will help suppress the population decline, we hope to we hope to establish Akita Prefecture as an affluent region where people gather.
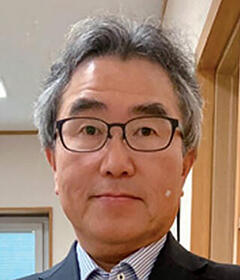
Yoichi Akagami,
Fellow, Akita Industrial Technology Center