Overview of development technology
The spread of electric vehicles is desired as an initiative toward carbon neutrality. In a step towards this, REE recovery technology that can reduce work time by 50% by simplifying the process without disassembling the motor of an electric vehicle or degaussing its magnet using the technology of dry smelting, which is a high temperature process, was established through an industry-academia collaboration between Waseda University and Nissan Motor Co. Ltd.
Background and history
In a general policy speech, former Prime Minister, Yoshihide Suga announced that carbon neutrality would be achieved by 2050, with emission reduction targets to reduce greenhouse gas emissions by 46% from 2013 to 2030 and reduce greenhouse gas emissions to zero by 2050. He added that concrete measures to achieve these goals should be implemented.
Japan's total CO2 emissions in 2019 was 1,108 million tons, and the total emissions from automobiles, including passengers and freight, accounted for 177 million tons (16%). It is hoped that the use of electric automobiles will reduce CO2 emissions. Japan has announced that it will achieve the sale of 100% electric vehicle by 2035. The world production of automobiles in 2019 was approximately 92 million units, and the production volume, including overseas production of Japanese automobile manufacturers, was 28.5 million units. In 2020, the total number of electric vehicles sold among Japan's passenger vehicles, including hybrids (HVs), plug-in hybrids (PHVs), electric vehicles (EVs), and fuel cell vehicles (FCVs), was 1.35 million units. Sales of electric vehicles are expected to increase in order to reduce CO2 emissions.
Motors are indispensable for driving and power generation in electric vehicles. Motors that do not use magnets have been adopted by Nissan Motor Co. Ltd.'s "Ariya"; however, many electric vehicle motors use neodymium magnets to improve the size and performance of the motors. REEs, such as neodymium, praseodymium, dysprosium, and terbium, are used in neodymium magnets. In recent years REEs have been produced in countries other than China such as Australia and Vietnam; however, the production of heavy rare earths dysprosium and terbium are exclusive to China. In addition, REE deposits may contain radioactive substances; therefore, treatment and management are indispensable for their smelting and refininment. Furthermore, toward the realization of carbon neutrality, the demand for REE in power-conserving home appliances such as wind power generation and air conditioners is expected to increase along with motors for electric vehicles. Therefore, the recycling of REEs is an urgent task, considering the uneven distribution of REE resources, environmental load, and the supply-demand balance.
Approximately 1.25 kg / unit of neodymium magnets are used in electric vehicles, and approximately one-third of the magnet mass is a REE component. If all of the vehicle production in 2019 were electric vehicles, 38,000 tons of REEs would have been required. However, it is predicted that 1,025,000 vehicles/year will be scrapped in 2030, 1,280 tons/year of waste neodymium magnets will be generated, and 430 tons/year of REEs will be wasted.
Currently, during recycling of motor magnets for electric vehicles, magnets are almost completely recovered from defective motors generated during their manufacturing process. Defective motors are disassembled into rotors, stators, and housings; thereafter, the stators are further disassembled to separate copper wire and iron scrap. Since the rotor has a strong magnetic force generated from the neodymium magnet, it is heated to 350-500 °C and decomposed after thermal demagnetization to recover the neodymium magnet. The recovered magnet is vacuum redissolved at high temperature to form a mother alloy for the magnet. In order to reuse neodymium as a raw material, there is a strict impurity target to reduce the carbon and oxygen concentrations in the magnets to 100 and 300 mass ppm or less, respectively. It is difficult to remove carbon via vacuum melting; hence, after crushing the recovered neodymium magnets and oxidizing the REEs and iron via roasting, the composite REE, containing neodymium, praseodymium, dysprosium, and terbium, is recovered by wet treatment as oxides and chlorides and regenerated as motor magnets for electric vehicles. Meanwhile, the recycling of REE from used motors from the market has not been achieved owing to lack of collection and transportation systems and high collection and separation costs.
Based on the current state of recycling of neodymium magnets, the authors have been conducting research on REE recovery from neodymium magnets using dry smelting technology using a high-temperature process that can demagnetize magnets and conserve labor costs for motor dismantling. Nissan Motor Co. Ltd. has set up the "Nissan Green Program 2022," which aim is to realize a carbon-neutral society by promoting electrification of vehicles, to eliminate dependence on new mining resources. They are actively working on recycling neodymium magnets in motors while reducing the amount of REE used in motors for electric vehicles. However, the current process requires manual heat treatment, disassembly, and removal of the motor. Hence, it is necessary to develop a simple and low-cost recycling technology to promote recycling in the future.
Waseda University's Kagami Memorial Research Institute for Materials Science and Technology currently has a large melting furnace weighing 100 kg, which can be used for testing on motors for electric vehicles. In 2017, Waseda University and Nissan Motor Co. Ltd. began developing a simple REE recovery technology using motor magnets for electric vehicles, thus presenting the collaboration of industry and academia.
Contents and results
As an example, Photograph 1 shows the rotor of the motor drive of an electric vehicle. The rotor is composed of iron-based materials such as electrical steel sheets and 1.75 kg of neodymium-iron-boron-based neodymium magnets. The concentrations of neodymium, praseodymium, dysprosium, and terbium in the magnet are 21, 5.0, 2.5, and 0.4 mass%, respectively, while the total REE concentration is 28.9 mass%, with the rest being iron and boron. Since the rotor exerts a strong magnetic force, thermal demagnetization is indispensable for dismantling the motor and recovering the neodymium magnets. In addition, the motor is designed robustly and manufactured to withstand the force and vibration generated during driving, making disassembly very difficult.
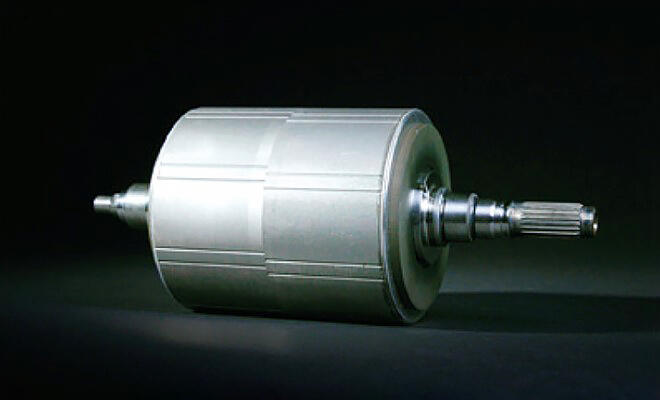
(Rotor) (Production: Nissan Motor Co. Ltd.)
Figure 1 shows the REE recycling process for the developed motor from electric vehicles.
This is a method of recovering REEs in a magnet as molten oxide (slag) using Na2B4O7flux without thermally degaussing or decomposing the rotor recovered from the motor of an electric vehicle.
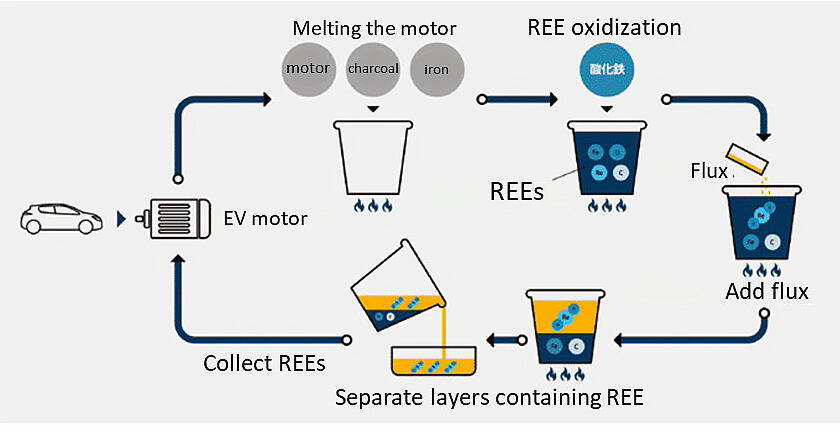
First, a rotor containing a neodymium magnet that has not been heat-demagnetized is melted with a carbonizing material at approximately 1,400 ° C. Next, iron oxide is added to selectively convert REE in the magnet into an REE oxide such as Nd2O3. The melting point of the REE oxide is extremely high, as represented by the melting point of Nd2O3 at 2,270 °C. Therefore, Na2B4O7flux is added to lower the melting point of the REE oxide to prepare a Na2B4O7-RExOy system (RE: Nd, Pr, Dy, Tb) molten slag. Iron, which is the main component of the rotors and neodymium magnets, reacts with the CO2 material to form a molten iron-carbon alloy. The slag has a lower density than the molten iron-carbon alloy; hence, it is separated into the upper part of the alloy in the vertical direction owing to the difference in density, and the melt-separated Na2B4O7-RExOy slag is recovered from the furnace. The REEs in the iron-carbon alloy separated from the rotor are 0.1 mass% or less. REE recovery from the magnet is possible at a recovery rate of 97-98%. Na2B4O7-RExOy-based slag is recovered as a high-purity REE composite oxide by applying the wet treatment of the current method.
Photograph 2 shows the REE composite oxide recovered by the wet treatment. The total concentration of REE oxides, such as neodymium, praseodymium, dysprosium, and terbium, was approximately 99.3 mass%. In addition, the theoretical recovery rate of REEs from rotors through melting and wet treatment is approximately 97-98%.
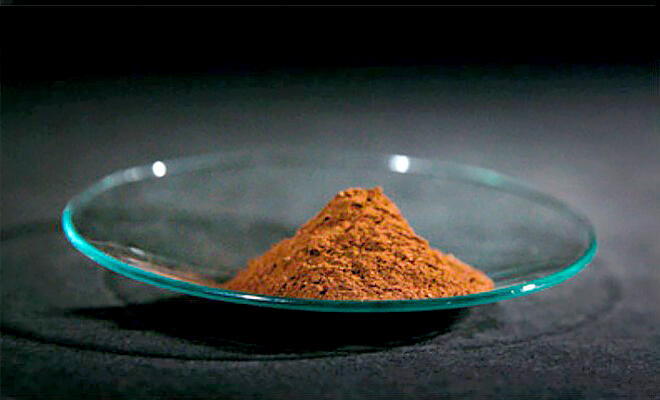
Thermal demagnetization and dismantling can be simplified using the pyrometallurgical method; thus, the work time for REE recovery from electric vehicle motors can be reduced by 50% compared to the conventional method. This technology also facilitates the processing of large quantities of used motors that are expected to be recovered from the market in the future.
Future policies and issues
A technology was established to recover REEs from actual motors using a 100-kg melting furnace from the university. In the future, to achieve practical use in the middle of the 2020s, the demonstration experiment is expected to continue outside the university, using a melting furnace that can process approximately 1000 kg. In addition, it is necessary to promote the construction of a scheme for collecting and transporting motors mounted on used electric vehicles in the city and establish an REE recycling system for electric vehicle motors.
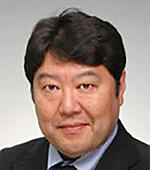
Katsunori Yamaguchi,
Professor, Faculty of Science and Engineering, Waseda University