The demand for rechargeable batteries is expected to grow, and there is a need to develop next-generation batteries with better safety characteristics. The Sulfide All-Solid-State Battery Subteam led by President Masahiro Tatsumisago of Osaka Metropolitan University and the Oxide Subteam led by Director Kazunori Takada of the National Institute for Materials Science (NIMS) are using solid electrolytes to develop safe, all-solid-state batteries with large capacities and high power.
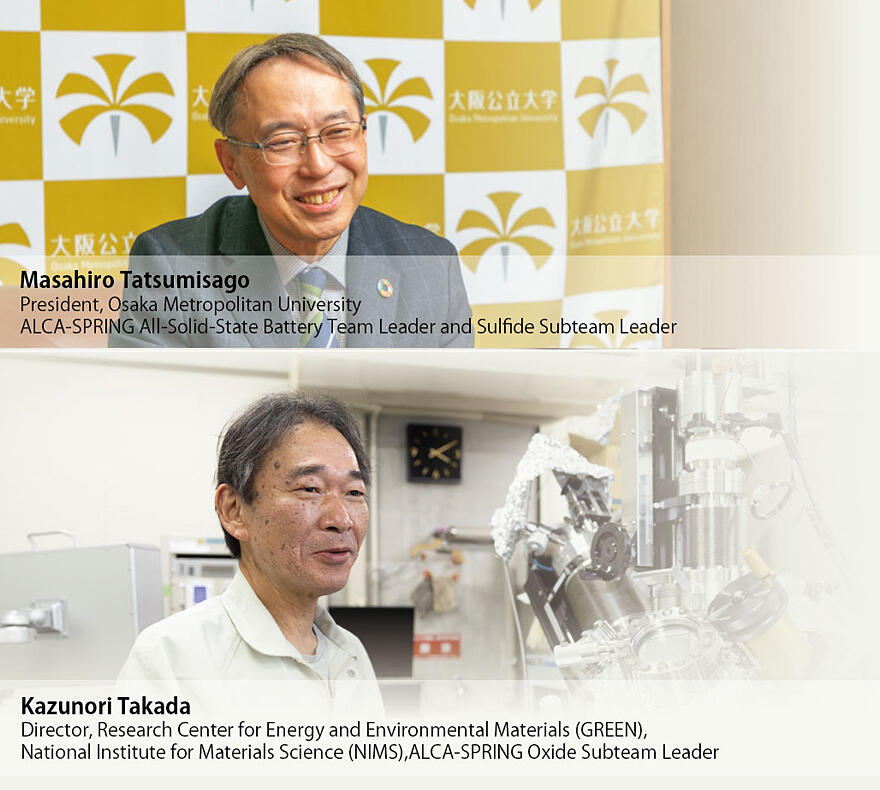
Stable performance that is resistant to temperature changes — Issues with ion migration speed
Compact, lightweight, and high-power lithium-ion batteries (LIBs) are used in smartphones and electric vehicles (EVs) and have become indispensable to our society.
However, LIBs use a flammable liquid as the electrolyte that fills the space between the positive and negative electrodes (cathode and anode), which can lead to ignition if the battery becomes hot or short-circuits internally. In order to achieve carbon neutrality, it is expected that larger-scale, higher-capacity rechargeable batteries will be needed in the future, which makes safety improvements an urgent issue.
In contrast, all-solid-state batteries, which use a solid electrolyte instead of an electrolyte solution, are attracting increasing attention (Fig. 1). ALCA-SPRING, under the leadership of Osaka Metropolitan University President Masahiro Tatsumisago, who is also the Team Leader, is developing this technology, focusing on sulfide and oxides, which are promising electrolytes (Fig. 2). The basic mechanism is the same as that of the LIB: ions move between the cathode and anode through the electrolyte, thereby creating an electrical current. The difference is that the solid electrolyte also acts as a separator between the cathode and anode.
Fig. 1: Schematic of an all-solid-state battery
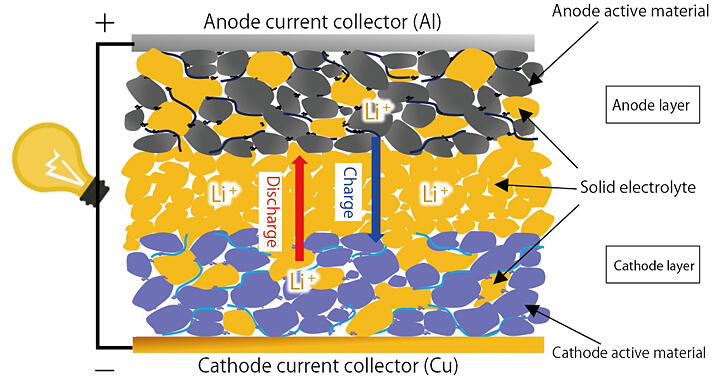
Fig. 2: Comparison between sulfide electrolytes and oxide electrolytes
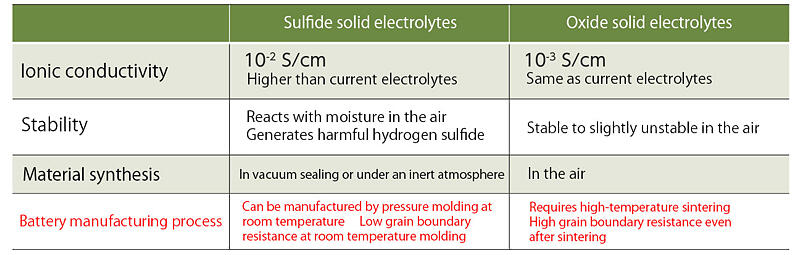
Additionally, because only lithium (Li) ions move within the electrolyte, all-solid-state batteries are less prone to side reactions and to deterioration. Tatsumisago explained, "Furthermore, when used in EVs or in harsh environments, all-solid-state batteries have the advantage of being resistant to temperature changes."
Because LIB electrolytes contain organic compounds, their viscosity increases at low temperatures, resulting in lower charge-discharge performance, and at high temperatures, the electrolyte evaporates and ceases to function as a battery. Therefore, a cooling system that takes up space is essential.
All-solid-state batteries have many advantages, but the challenge for their practical application is how to move ions at high speeds in a non-flowing solid.
Additionally, in order to achieve high battery performance, the electrode's active material and the electrolyte must be bonded without gaps. "Unlike with liquids, it is difficult to keep solids in constant contact with each other.
If they are not bonded well, then the active material will expand and contract, causing the interface to peel and the electrode to crack." To solve these problems, all-solid-state batteries are currently being researched and developed around the world.
Understanding the degradation mechanism associated with heat generation: Expectations for application to other battery materials
The Sulfide Subteam, led by Tatsumisago, was initially developing two types of batteries. The first was a 'first-generation all-solid-state battery,' which aims to solidify current LIBs, and the other was a 'next-generation all-solid-state battery,' that looked ahead to the future. The former employs a ternary system that uses graphite for the anode, nickel (Ni), manganese (Mn), and cobalt (Co) oxides for the cathode, and a sulfide-based electrolyte. The latter uses Li, which is expected to have high energy density, for the anode, a sulfur-based active material for the cathode, and a sulfide-based electrolyte.
The former project has made steady progress in research and development, and, as the development of solid electrolytes with the world-class conductivity and optimal electrode structure have been clarified, the project was transferred to the 'SOLiD-EV Project' by NEDO in 2018.
In the five years since then, the Project has been focused on the next-generation sulfide all solid-state batteries.
The key to all solid-state batteries is the development of solid electrolytes with high ionic conductivity. To achieve this, it is necessary to understand the state and behavior of the electrolyte. To this end, Tatsumisago and his colleagues focused on the inorganic solid electrolyte Li2S-P2S5 (LPS), a compound of lithium sulfide (Li2S) and diphosphorus pentasulfide (P2S5).
By using a transmission electron microscope (TEM) to directly observe the electrode's state before and after heating, they were able to understand the characteristics of the crystallization behavior of the glass and the formation process of the superionic conducting phase (Fig. 3).
Fig. 3: High-resolution electron microscope image of glass-ceramic
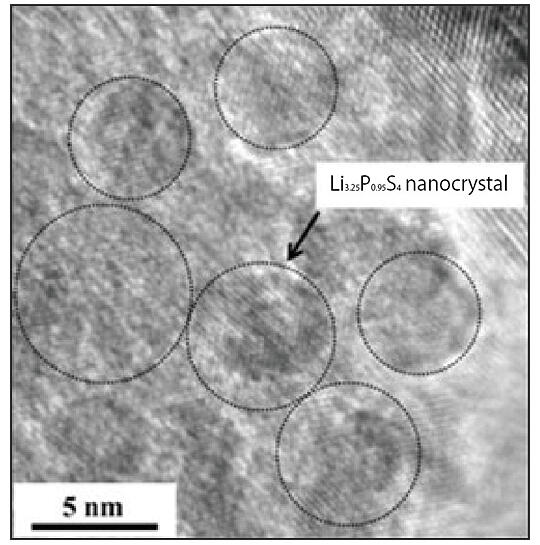
The importance of evaluating thermal stability was also emphasized. For practical usage, it is necessary to suppress heat generation and ignition and to ensure safety. Since heat generation can shorten battery life, it is essential to evaluate a battery's heat generation behavior and to understand the factors behind it. Therefore, the focus was on a cathode composite consisting of LPS and LiNi1/3Mn1/3Co1/3O2 (NMC). In-situ TEM observations were used to analyze the thermal stability of the materials, possible chemical reactions, and the factors that contribute to the exothermic (heat generating) reaction of the cathode composite.
In doing so, it was found that the exothermic reaction of the NMC-LPS cathode composite may involve the exothermic reaction associated with the crystallization of Li4P2S6 and Li2S, which are formed by the decomposition of Li3PS4. Discussing this achievement, Tatsumisago stated, "We expect that this method of analyzing heat generation behaviors can be applied to other battery materials." (Fig. 4) In the future, he plans to further clarify the factors behind the exothermic reaction by calculating the activation energy in the crystallization process.
Fig. 4: Decomposition reaction of LPS in the NMC-LPS cathode composite after charging
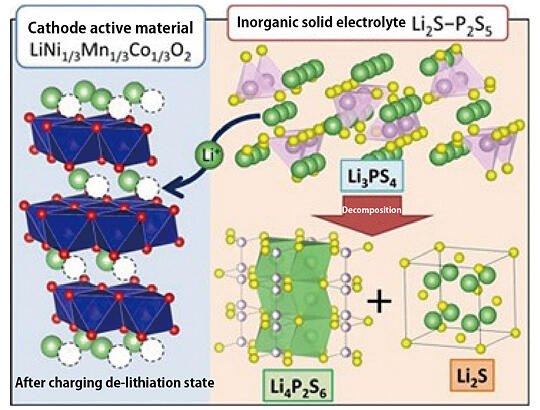
New cathode dramatically improves capacity: No deterioration even after 2000 charge-discharge cycles
Tatsumisago and his team have also discovered a new solid electrolyte. They had previously found high ionic conductivity in LGPS sulfide solid electrolytes, which are compounds of Li, P, S, and germanium (Ge). Furthermore, in a new composition containing tin and silicon, they discovered a superionic conductor with an ionic conductivity of 11 siemens per centimeter (S/cm), which is comparable to that of liquid electrolytes. In a superionic conductor, ions can move around in the solid like in a liquid. It has also become clear that the problems of existing materials can be solved, and, if the diversity of solid electrolyte substance groups expands, it is expected that the range of battery designs will also greatly expand.
For sulfide lithium-sulfur all-solid-state batteries, the team developed a cathode that combines a Li2S-based solid solution and a sulfide solid electrolyte, which dramatically improved the cathode's capacity and life. "No capacity deterioration was observed even after 2000 charge-discharge cycles." (Fig. 5). Tatsumisago will continue to work with a variety of organizations to realize next-generation batteries that are safe and have high energy density.
Fig. 5: Charge-discharge curves of cathode composite and all-solid-state batteries developed by ALCA-SPRING
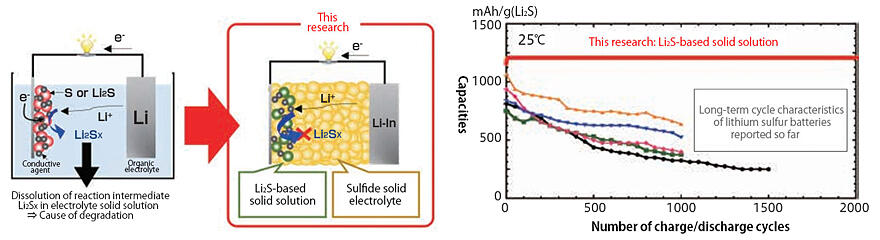
Oxide solid electrolytes can be synthesized in the air, but they are hard and brittle make bonding an issue
Another sub-team for all-solid-state batteries, the ALCA-SPRING Oxide Subteam, is led by Director Kazunori Takada of the Research Center for Green Research on Energy and Environmental Materials (GREEN)at the National Institute for Materials Science (NIMS). Oxide electrolytes are more chemically stable than the sulfide batteries and are easier to synthesize and manage in the atmosphere. For example, unlike with sulfide electrolytes, there is no concern that toxic gases will be emitted when reacting with water, so process costs can be reduced.
Takada stated, "The problem with oxides is that their ionic conductivity is one order of magnitude lower than that of sulfides, and that they are a hard, brittle material that is difficult to bond to electrodes." High-temperature sintering is essential for bonding, but, during this process, interdiffusion of elements between the electrode and electrolyte causes impurity phases, which increases the internal resistance. Takada and his team are working on two approaches to solve these problems. One method is to increase the ionic conductivity of an electrolyte with high bonding properties, and the other is to increase the bonding properties of electrolytes with high ionic conductivity.
Li superionic conductor (LISICON) materials are promising for the former, and garnet oxides are promising for the latter. While changing these compositions, he is working on developing electrolytes with high performance.
World-first operation of a bulk battery at 60 ℃ — Towards construction and utilization of a search database
One of the achievements that brought about technical changes was the introduction of a new bonding method. Until then, sol-gel and flux methods had been used, but, because solutions of precursors were applied and sintered one layer at a time, it was labor-intensive and did not provide high accuracy. To solve this problem, Takada and his colleagues established a unique bonding technology that can be applied to the lamination method for multilayer ceramic capacitors. Efficiency and accuracy were greatly improved by making the electrolyte into fine powder, layering it, and then sintering it all at once.
The development of 'Operando CT-XAFS,' an electrochemistry computed tomography X-ray absorption fine structure (XAFS) method, has also greatly advanced the research. "This is a new method that enables 'in-situ' observation of the complex behavior of particles in electrodes. It has also let us clarify the causes of failure and problems, enabling us to respond quickly and accurately," said Takada.
They are already seeing results. With the garnet electrolyte, the team succeeded in fabricating a battery by sintering at a low temperature of 400 ℃. "The low sintering temperature suppresses chemical reactions with the active material, which makes it possible to create batteries with greater stability." At the same time, they were the first in the world to succeed in operating a bulk battery at 60 ℃ (Fig. 6). After that, they also managed to realize operation at room temperatures of 20 to 25 ℃. The team has also developed a highly stable LISICON electrolyte and succeeded in assembling a full cell using the green sheet method, which fits mass-producible (Fig. 7).
Fig. 6: LTO/NMC battery using garnet fine particles
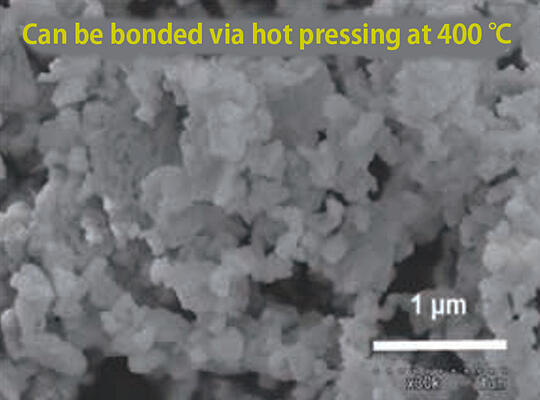
Fig. 7: LLZT−LGVO−LBO composite solid electrolyte green sheet
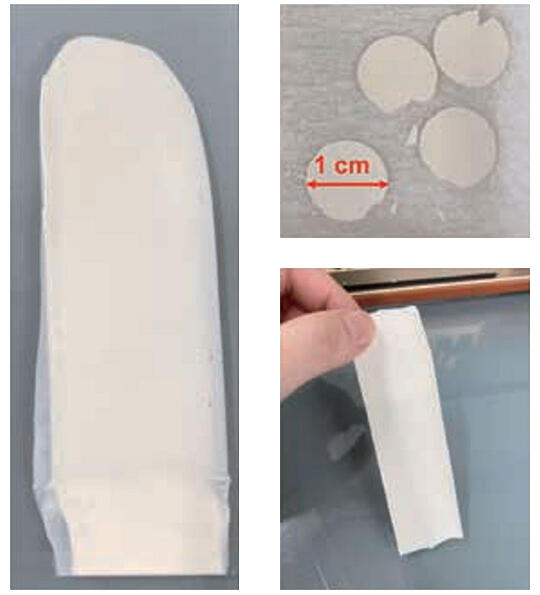
Despite having reported numerous successes, Takada remains cautious. He says that the oxide batteries are still an uncharted area, and that there are still two or three large hurdles that need to be overcome in the future. Moreover, there is a long history of oxide battery research, and he expects more difficulties than ever before in searching for systems that have already been extensively explored.
On the other hand, the fact that oxide batteries have a long history means that they have also accumulated an enormous amount of research data. "We have established the ALCA-SPRING Solid Electrolyte Exploration Task Force and are now in the process of building a database that includes negative data. We hope that breakthroughs will be made by using big data," said Takada, who is looking beyond ALCA-SPRING.
(Article: Kazuyuki Katayanagi; Photography: Hideki Ishihara)