In the segment 'A Look Around Innovation,' we introduce R&D sites that have led to social implementation. In this installment, we introduce Professor Minoru Osada of the Institute of Materials and Systems for Sustainability (IMaSS) at Nagoya University. Osada is engaged in research and development that contributes to environmental and energy technologies. This also includes the development of new functional nanosheets, facile device manufacturing, and innovative electronic materials /devices.
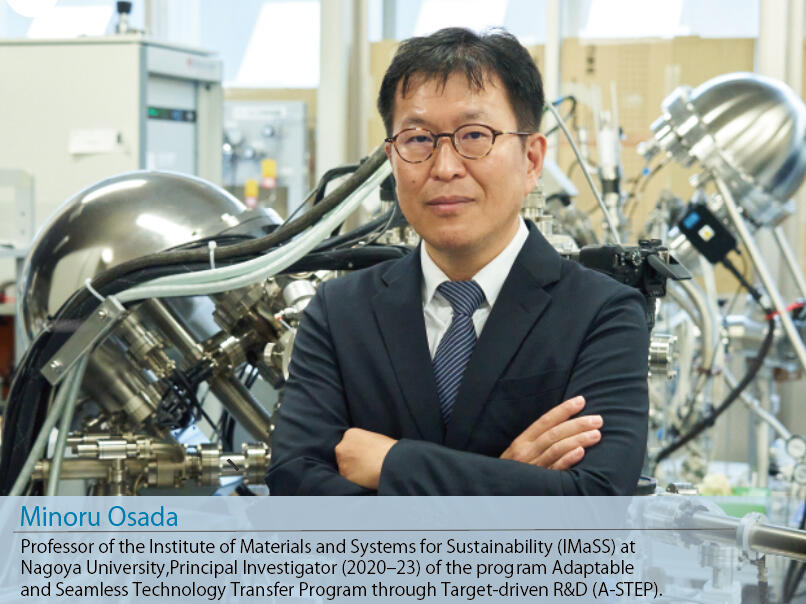
Bridging new processes to create materials that will benefit the world
IMaSS at Nagoya University aims to contribute to the realization of an environmentally harmonious and sustainable society through research and development ranging from introducing advanced materials/device technologies to creating system technologies. The Institute is the largest interdisciplinary research organization at Nagoya University, with the goal of creating new academic fields and establishing a new academic framework.
Osada has been working on the research and development of 'nanosheets' at IMaSS since 2018. A nanosheet is a sheet-like material with a thickness of only a few atomic layers, i.e., approximately 1 nm (one billionth of a meter). Its lateral dimensions are thousands to tens of thousands of times larger than its thickness. Depending on the type and structure of their constituent atoms, nanosheets can exhibit excellent properties such as high electron mobility high permittivity, and high catalytic activity and can also be applied to functional thin films.
Osada focused on three research themes, namely, materials, processes, and devices, in the A-STEP project 'Development of Innovative Dielectric Materials and Devices Using Nanosheet Technology.' Specifically, he focused on the synthesis of new functional nanosheets, development of industrial level thin film fabrication methods, and development of energy storage devices. He emphasized the importance of considering the entire process from material development to device integration: "To fabricate materials that benefit society, I believe that the ultimate goal should be to produce functional devices by bridging new processes."
Nanosheet synthesis at low temperatures — Confirmation that ferroelectricity is maintained/Ferroelectricity down to the critical thickness
For the development of nanosheets, the aim was to synthesize molecularly thin oxide nanosheets that exhibit 'ferroelectricity,' a property enabling electricity storage. Ferroelectricity, which allows a material to store a large amount of electricity, is essential for electronic components, etc. In conventional materials, reducing the thickness leads to the disappearance of ferroelectricity, a phenomenon known as the 'size effect.' For barium titanate (BaTiO3), a typical ferroelectric material, it is difficult to synthesize nanosheets by the conventional synthetic method. Therefore, it was necessary to develop a new synthetic method.
Therefore, Osada focused on the high reactivity of nanosheets. 1 nm thick titanium oxide (TiO2) nanosheets were used as templates, guiding tailored synthesis of BaTiO3 nanosheets. He successfully synthesized BaTiO3 nanosheets using a mixed solution of water and ethanol. The result is the thinnest free-standing BaTiO3 nanosheet ever made. It was also confirmed that the ferroelectricity was maintained even down to a thickness of 1.8 nm and disappeared at a thickness of 1.4 nm (Fig. 1).
Fig. 1: Synthesis of BaTiO3 nanosheets and investigation of their ferroelectric property
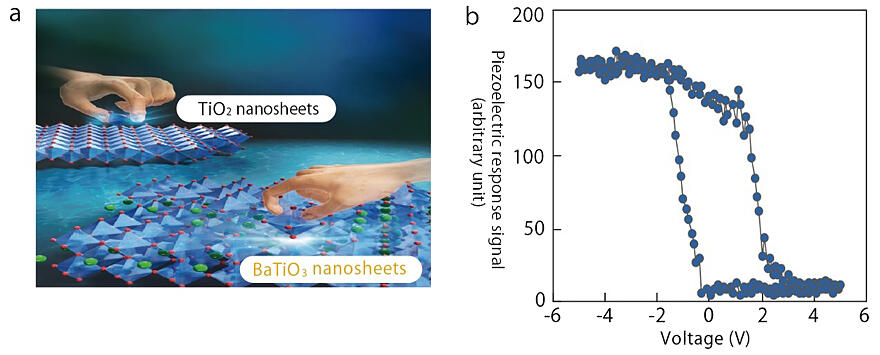
Generally, the synthesis of BaTiO3 requires a calcination process that requires temperatures of 1000℃ or higher. In contrast, Osada synthesized BaTiO3 nanosheets at a low temperature of 60℃ using solution-based process. "We knew that this method could be used to synthesize BaTiO3 at lower temperatures, although we did not expect it to be so low. It was difficult to overcome our preconceived notions, and extensive trial-and-error was required," he said, looking back at the difficulties he faced at the time.
'Egg of Columbus' moment: Success in establishing an automated film deposition method
The goal in developing the nanosheet fabrication process was to achieve facile and scalable thin film deposition method. Generally, nanosheets are deposited using the Langmuir−Blodgett method, which involves spreading an aqueous colloidal solution of nanosheets on a shallow tray and accumulating the sheets spread at the air-liquid interface to form a thin film. However, this method requires skillful manipulation, complex condition setting, and large amounts of solution. Furthermore, the fact that it takes approximately 1 h to form a monolayer has been a significant bottleneck for industrialization.
Furthermore, the drop-casting method, in which an aqueous colloidal solution is dropped on a substrate and dried, produces a non-uniform film. In the process of developing another method, Osada's research team accidentally discovered a possible solution. "A student once exclaimed, 'What a waste of solution,' and immediately used a pipette to aspirate the solution that had spilled. Consequently, a highly organized film was formed within seconds. It was truly a 'Egg of Columbus moment," explained Osada. They immediately analyzed this phenomenon, and based on the results, succeeded in establishing an automated drop and aspiration process using a robot (Fig. 2). This automated film deposition method received significant attention at a New Technology Presentation Meeting run by JST. He also received inquiries from companies for collaborative research.
Fig. 2: Facile solution-based thin film deposition of 2D nanosheets
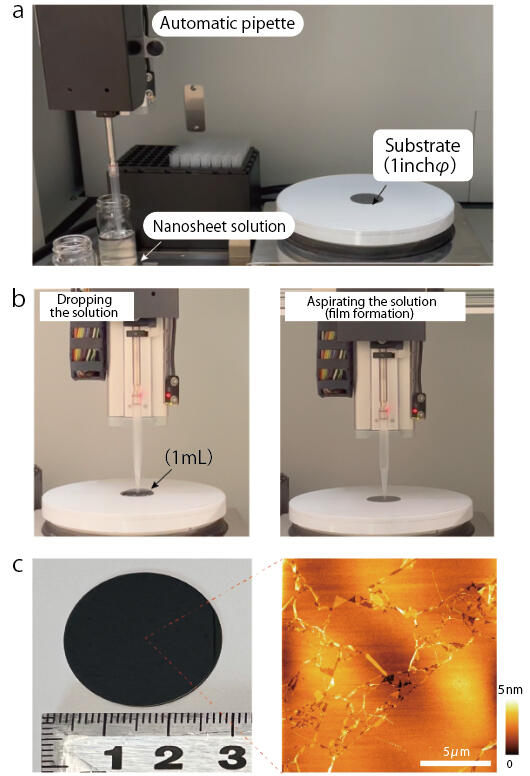
(b) The film was formed by dropping the solution onto the substrate using an automatic pipette, followed by aspirating the solution.
(c) Characterization by atomic force microscopy (AFM) confirmed that the nanosheets were densely arranged like playing cards.
Nanosheet devices with the highest energy storage performance yet seen
The ultimate goal of A-STEP is to develop 'dielectric capacitors,' which are attracting attention as a new energy storage device. Dielectric capacitors have many advantages, such as a short charging time of only a few seconds, a long life, and a high-power density. However, existing materials are limited by the amount of electric field they can handle.
To go beyond conventional dielectric materials, Osada used new dielectric nanosheets with molecular level thicknesses (1.5 − 3 nm). These nanosheets exhibited high dielectric performance as well as good insulating properties, achieving the highest energy density (174−272 J/cm³) ever recorded. This is equivalent to ∼10 times the energy density of conventional dielectric materials and comparable to that of lithium secondary batteries (Fig. 3). Additionally, it was confirmed that the nanosheet remained stable even at temperatures as high as 300 ℃. In the future, this nanosheet is expected to be applied to all-solid-state energy storage devices, such as power boosters for electric vehicles.
Nanotechnology not only enriches society by significantly improving the functions and characteristics of materials but also contributes substantially to environmental and energy technologies as it requires very few materials for device fabrication. "Nanotechnology is very significant for Japan, a country with limited resources. In this regard, I believe this is a visionary technology that brings new value to society," said Osada with a smile.
Fig. 3: Comparison of the nanosheet capacitors with other energy storage devices
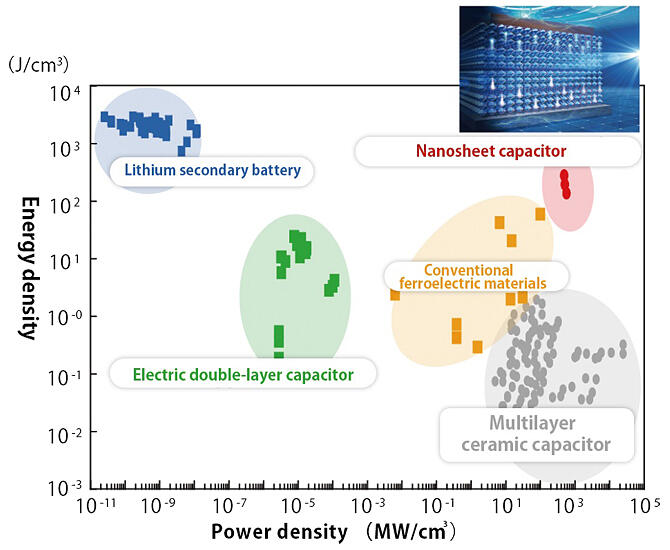
(Article: Manami Yokoi, Photography: Akihiro Ito)