Biomass resources play a key role in promoting low-carbon energy. In Japan, microalgae, which are photosynthetic algae and useful as a material for various products, are currently looked at through expectant eyes. They have been used to date as materials for functional food and cosmetic products. Rapid technological developments are being made to exploit microalgae to produce bio-jet fuel in Japan. JST News interviewed Senior Professor Hiroshi Mitani and Professor Emeritus Shigeyuki Kawano of the Graduate School of Frontier Sciences at the University of Tokyo and Professor Hiroshi Yamamura of the Department of Integrated Science and Engineering for Sustainable Societies, Faculty of Science and Engineering at Chuo University, who are pursuing the possibility of developing bio-jet fuel from microalgae through industry-academia collaboration.
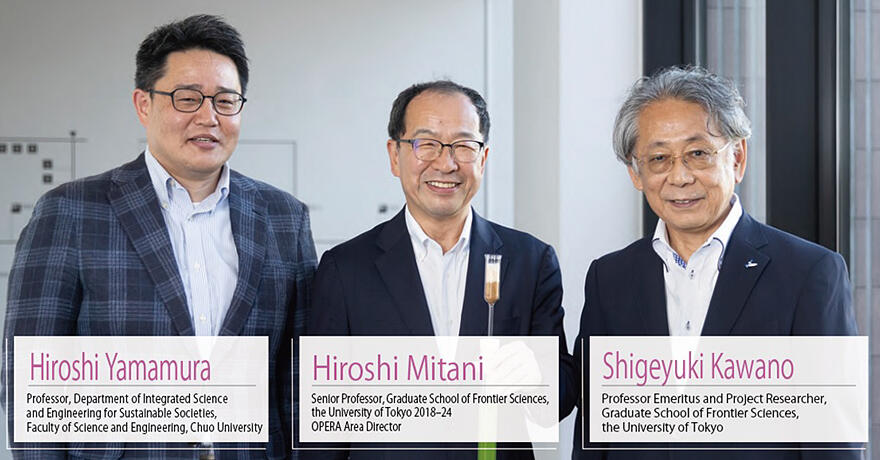
Last resort for low-carbon aviation fuel: Urgent need to establish SAF production system
In 2024, it was reported in the Japanese news that plans to launch new international airlines and increase international flights had been abandoned. One reason is that there isn't sufficient aviation fuel available from domestic sources. Resource-poor Japan relies on imported energy. As the global fight over energy intensifies, Japan continues to be outbid by other countries, partly due to the weak yen. Reducing carbon dioxide (CO2) emissions is also an inevitable issue for aviation fuel. With the imminent need for a transition to low-carbon aviation fuel, bio-jet fuel made from biomass and waste cooking oil, known as "sustainable aviation fuel (SAF)," is attracting attention as a last resort.
The International Air Transport Association (IATA), an association of commercial airlines, approved a new goal of "net zero CO2 emissions by 2050" at its annual meeting in 2021. In 2022, the International Civil Aviation Organization (ICAO), an international organization made up of national governments, adopted a long-term goal of virtually zero CO2 emissions by 2050. These decisions have changed conditions dramatically. Japan also established a goal of replacing 10 percent of fuel usage by Japanese domestic airlines by SAF as of 2030. Therefore, the establishment of an SAF production system is an urgent task for the country.
The commercialization of SAF has gradually begun in Japan. The Ministry of Economy, Trade and Industry (METI) has forecasted Japan's SAF use of 1.72 million tons in 2030 (Figure 1) and proposed a target SAF supply equivalent to at least 5% of the greenhouse gas emissions from jet fuel domestically produced and supplied in fiscal year 2019. A dramatic increase in production will be required to achieve this goal. Mitani and Kawano have been working with 14 universities, 4 national research institutes, and 24 private companies on this challenging issue under JST's OPERA Program, and warn that individual companies' efforts alone will not be enough to quickly establish a SAF production system in time.
Figure 1:CO2 emissions from the aviation industry and expectations for sustainable aviation fuel (SAF)
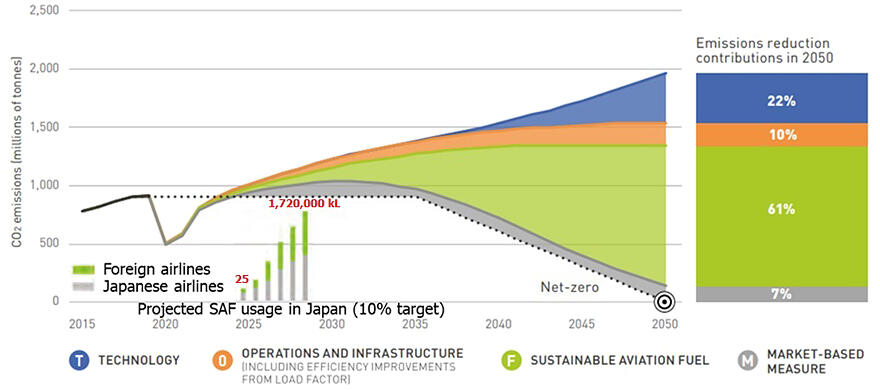
(Figure 1 shows the Waypoint 2050 line graph with a bar graph from the Civil Aviation Bureau of the MLIT.)
"Refinery" to increase efficiency: From functional foods to feedstuffs and fuels
Currently, the main SAF distributed worldwide is bioethanol, which is derived from sugarcane and corn. Japan has neither abundant biomass resources nor sufficient lipid raw materials, such as waste cooking oil, from domestic sources. Therefore, this project is aimed at producing useful substances from microalgae and creating a biorefinery process integrating these substances. The parties involved in the project have been focusing on research and development to produce SAF from microalgae for the last 2 years.
Microalgae are algae as small as 5-50 micrometers, such as euglenids and Chlorella. Because they have chloroplasts, they can produce organic matter through photosynthesis as long as sunlight, water, and CO2 are available. Microalgae have also attracted attention as a useful class of biomass because their yield per area is an order of magnitude higher than that of seed plants. Mitani explained the overall concept of the project as follows: "We have been working comprehensively with microalgae, believing that microalgal refineries are possible for various products ranging from functional food, cosmetic and clothing materials to feed, fertilizer, and fuel" (Figure 2).
Figure 2:Biomass refinery system
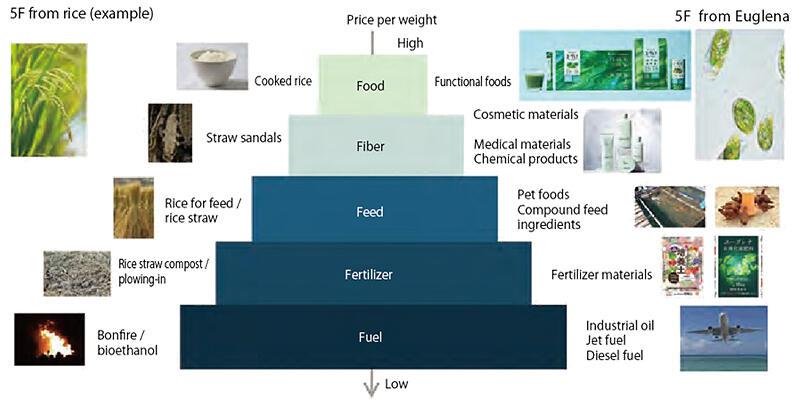
(Figure provided by Euglena)
A "refinery" refers to a method of producing a variety of products through refining a single raw material. For example, in the context of petroleum processing, crude oil is being refined into petroleum. "Oil refinery" is a method of improving the total production efficiency of the whole process from crude oil. Similarly, this project intends to secure overall profitability by producing high-value-added functional foods and cosmetic materials from biomass in the process of SAF production, thereby reducing the cost of the process. With the aim of early realization of SAF, the project developed a wide range of technologies, including breeding, cultivation, and recovery of microalgae, oil extraction, and utilization of the residues.
Chlorella culture with 70% oil content using sugar beet molasses as a nutrient source
Can oil be obtained from microalgae in the first place? In regard to this, Mitani explains, "There are various types of vegetable oil, such as sesame oil and rapeseed oil. Algae are also photosynthetic organisms, so they can produce oil, starch, and other substances that plants can produce." Depending on the environment, algae select whether to store the nutrients they produce from atmospheric CO2, such as starch or oil. If humans can successfully control this choice, strains accumulating large amounts of oil can be bred.
In the second half of the project, the goal was to scale up SAF production. First, based on the strains selected from the library comprising 3,000 strains of microalgae collected mainly by the Microbial Culture Collection of National Institute for Environmental Studies (NIES Collection), productive oil-producing strains were bred using various methods such as heavy-ion beam irradiation and genome editing. When the bred Chlorella strains were mass cultured in an outdoor facility, the oil production by the strains reached an oil content per biomass of 66 percent and an oil productivity per liter of culture medium of 0.59 grams per day as of June 2024, which ranked first in the world for outdoor autotrophic culture of microalgae.
To further increase production efficiency using these strains, Kawano examined autotrophic culture, in which microalgal growth depends on photosynthesis, and also heterotrophic culture, in which biomass-derived sugars are added. Kawano and his colleagues focused on sugar beet as this sugar source. "Sugar beet," also called beet, is used to make sugar and is grown only in Hokkaido in Japan. Its production volume is 4 million tons, and is 2.4 times the production of potatoes, the second largest in Hokkaido. In the sugar refining process, molasses, which contains sugar not crystallized as refined sugar, is obtained. Kawano wondered "if there was any way to make effective use of this blackstrap molasses (molasses)."
Glucose and fructose are the main sugar sources that microalgae can use. Few algae can utilize sucrose as is, which is the main component of white sugar. Chlorella also cannot break down sucrose. Therefore, Kawano hydrolyzed sucrose with acidic water and used the glucose and fructose products to culture Chlorella. The result showed that the yield was more than twice as much as commercial molasses yield. In heterotrophic cultures to which such sugar source is added, the oil content of Chlorella can reach 70% (Figure 3). If the content is too high, the Chlorella cells float in water, and the algae cannot be collected properly, so fine adjustment is important.
Figure 3:Micrograph of heterotrophically cultured Chlorella.
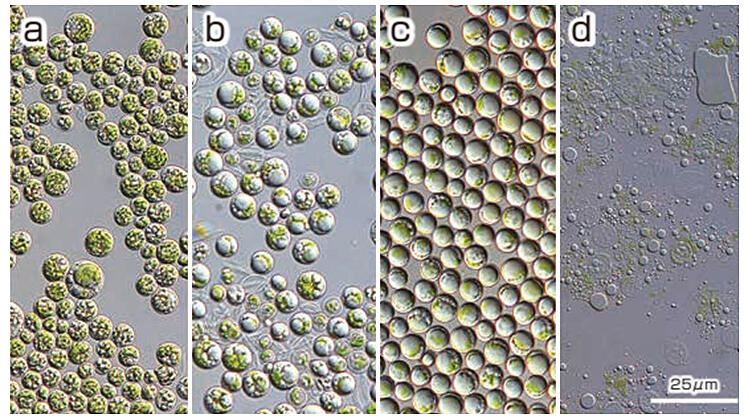
Despite its low oil content, Scenedesmus has been reported to reach a biomass yield of 286 grams per liter of culture medium, showing the high potential of heterotrophic culture of microalgae. Kawano commented, "We could confirm that a realistic method of SAF production is to combine heterotrophic culture, which allows stable mass production, and low-cost autotrophic culture." Sugar beets have high productivity and CO2 absorption, and molasses are always produced during refining. Currently, Kawano is conducting joint research with the Hokuren Federation of Agricultural Cooperatives and Nippon Beet Sugar Manufacturing Co., Ltd. on heterotrophic cultivation of microalgae using sugar beet molasses as a sugar source.
Development of "non-porous hollow fiber membrane:" Cost reduction by decreasing CO2 diffusion
To improve productivity and reduce production costs in an autotrophic system, Yamamura is working with Mitsubishi Chemical Corporation to develop technology to dissolve CO2, which is necessary for photosynthesis, in water using a membrane without waste. When cultivating algae outdoors, it is common to dissolve CO2 into the water tank using CO2 cylinders or factory exhaust gas because spontaneous absorption of CO2 from the atmosphere is not enough to increase productivity. However, research led by Yamamura has shown that 80%-95% of CO2 blown into the culture media is not absorbed and returned to the atmosphere.
"Under such conditions, it is questionable if algae cultivation can be said to contribute to carbon neutrality, and additional costs such as CO2 cylinders are also necessary," says Yamamura. Furthermore, after 2030, the supply of CO2 will decrease, and prices will increase, partly due to the shutdown of petrochemical plants in Japan. Since the efficient use of CO2 provides both environmental and cost advantages, Yamamura and his colleagues developed a technology to dissolve CO2 gas in water thoroughly without returning it to the atmosphere and use dissolved CO2 completely without waste.
CO2 is only slightly soluble in water and is more prone to diffuse into the atmosphere when the liquid concentration is higher. The aim is the development of modules and supply systems to overcome these physical laws. In the development process, the CO2 concentration suitable for cultivation differed for each microalgal strain, and the control of CO2 levels was added to the development goals. As a result of this effort, a non-porous hollow fiber membrane, which looks like a collection of fine fibers, was created. They confirmed that diffusion into the atmosphere was reduced when this membrane was submerged in an aquarium tank, and CO2 was supplied from a cylinder.
Specifically, the amount of CO2 absorbed by the algae has been improved by about four-fold compared to conventional methods, and the absorption rate could be increased by up to 36 percent with the external circulation method (Figure 4). This alone is estimated to reduce costs by approximately 300,000 yen per ton of microalgae produced. Outdoor tests have been conducted using actual factory exhaust gases, and effectiveness has been proven. Currently, they are also developing a closed culture system to release no CO2 into the atmosphere and use CO2 completely without waste.
Figure 4:Non-porous hollow fiber membranes for improving CO2 utilization efficiency
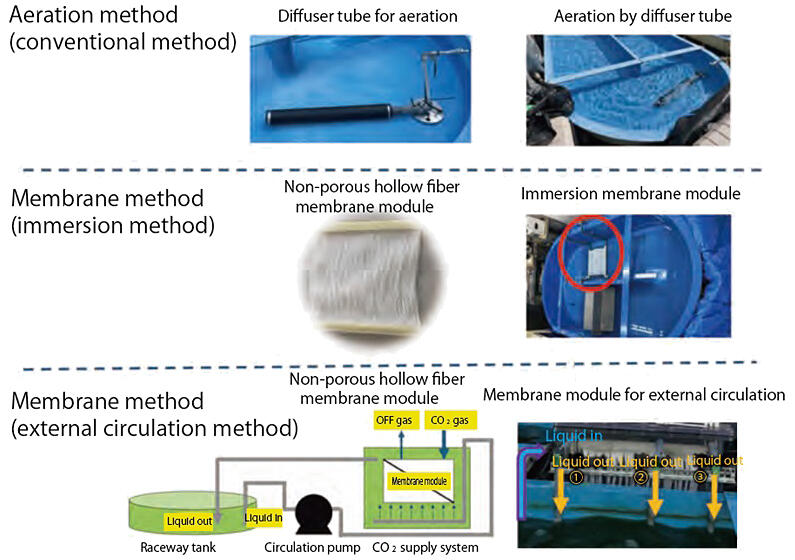
Distribution of stocks by consortium: Expectations include use in feed development
In addition to the technology for efficient cultivation of microalgae suitable for fuel production, Kawano and his colleagues also conducted research to efficiently extract oil from the cultivated algae. As a result, three methods were established: oil expression, extraction with methanol and methyl tert-butyl ether, and extraction with hexane. They also confirmed that the components of the extracted oil satisfy the quality requirements for SAF raw materials. Within the OPERA consortium, a mechanism has also been established for the secondary distribution of strains held by the National Institute for Environmental Studies to institutions and companies intending to conduct applied research on microalgae. This mechanism contributed to various results, including the development of functional foods, livestock feed, and aquatic feed.
For the effective use of microalgae residues after oil expression and extraction, they have also developed technologies through JST's OPERA Program to make strong bioplastics and functional nanofiber chemical products by mixing the residues with plasticizers. The oils and fats from microalgae actually have great potential for food use as well as SAF. With the current high price of olive oil, microalgal oil is expected to be utilized as a food material. "The fatty acid composition of Chlorella oil is between that of palm oil (rich in saturated FAs) and olive oil (rich in polyunsaturated FAs), so we could start with use of Chlorella oil in food, and then use the waste cooking oil to make SAF," said Kawano.
Mitani also provided examples of utilization, "The scale-up of microalgae industry is expected to lead microalgae use in purification of sewage and wastewater and exhaust gas treatment. Microalgae can also be transformed to produce proteins suitable for feed and other products." Kawano also emphasized, "The success of land-based cultivation of seaweed using single cell cultures of the marine alga Monostroma nitidum brings a new perspective to the Japanese fisheries industry" (Figure 5). Moving forward, further production increases through technological innovations such as CO2 supply by non-porous hollow fiber membranes are desired. The increased production will not only contribute to CO2 reduction but also provide new perspectives for blue carbon research.
Figure 5:Land-based Ulva prolifera cultivation
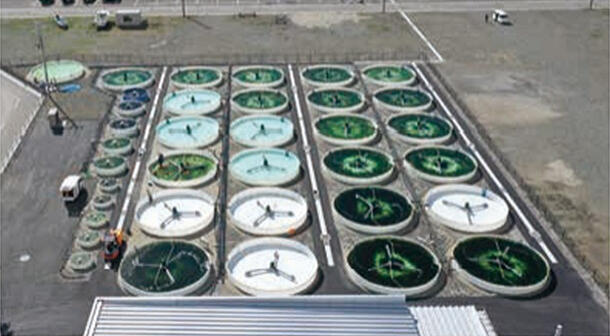
OPERA ended in March 2024, but Mitani, Kawano, and their colleagues recently launched the "Algae Photosynthesis Innovation Consortium" to maintain the community built up by OPERA. They intend to broaden the base of research for the utilization of microalgae through continuous and strategic research and development and the accumulation of the results. In addition to the early commercialization of SAF, further development of technologies to effectively utilize microalgae is expected.
(Article: Yuko Sakurai, Photography: Hideki Ishihara)
