In the segment 'A Look Around Innovation,' we introduce research and development (R&D) sites that have led to social implementation. In the 18th installment of this series, we introduce the efforts of Professor Shinya Furukawa of the Graduate School of Engineering, Osaka University. He is working to develop and commercialize an innovative multi-element alloy catalyst for propylene production via effectively utilizing carbon dioxide (CO2) to realize a carbon neutral society.
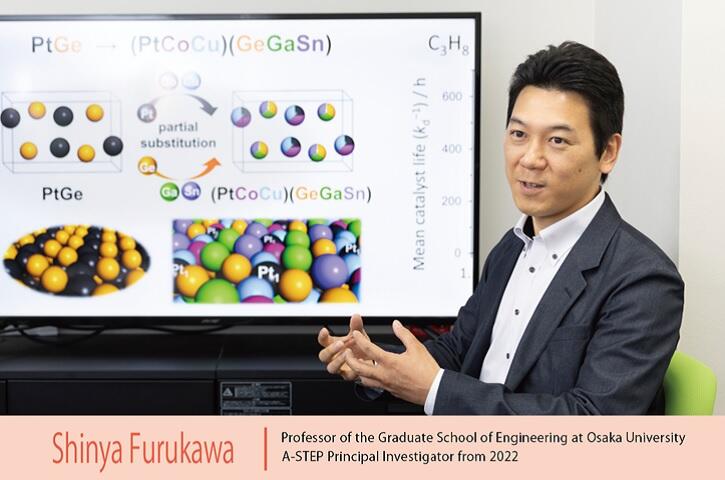
Generation of nanosized metal particles with high durability and 99.6% selectivity
When JST News stepped into the laboratory of Professor Shinya Furukawa of the Graduate School of Engineering at the Suita Campus of Osaka University, they found glass laboratory equipment lined up in neat rows. When one hears the word "alloy" catalyst research, one may imagine a furnace for melting metals, but Furukawa laughed, "When we say alloy, it does not mean that we are making structural metal materials, such as brass or stainless steel. Rather, we are chemically generating nanosized metal alloy particles." A catalyst is a substance that facilitates a chemical reaction. Even chemical reactions that only proceed very slowly under normal conditions can be accelerated using an appropriate catalyst.
For example, propylene is a raw material for various chemical products, such as plastics, fibers, synthetic rubber, and pharmaceuticals. Propylene is produced through a "dehydrogenation reaction" using propane contained in natural gas and liquefied petroleum gas as the raw material. Currently, to accelerate this dehydrogenation reaction, a platinum-tin alloy catalyst formed on the alumina surface is used. However, when the reaction is performed at high temperatures of >600℃, a side reaction yields tiny carbon particles called "soot." Therefore, as the reaction proceeds, soot covers the catalyst surface, degrading performance. Developing a regeneration treatment process to remove adhered soot is critical.
To solve this problem, Furukawa is working on developing a "multi-element alloy catalyst" that combines multiple elements. The functions required of a catalyst are "not only promoting reactions but also suppressing unwanted side reactions and ensuring the long-term stability of the desired reactions." From two-element alloy catalysts that have been the main focus of his research, Furukawa has been working on three- and four-element multi-element alloy catalysts to meet the diverse needs of the chemical industry, which is becoming increasingly sophisticated. It all started back in 2019.
At the time, Furukawa was an Associate Professor of the Institute for Catalysis at Hokkaido University. He was working on developing a new catalyst for propane dehydrogenation as part of the JST Presto project and developed a three-element alloy catalyst by adding lead to platinum and gallium alloy nanoparticles. This new catalyst exhibited high durability and a propylene selectivity of 99.6% because lead on the catalyst surface suppressed carbon deposition (Figure 1).
Figure 1:Durability of propane dehydrogenation catalysts
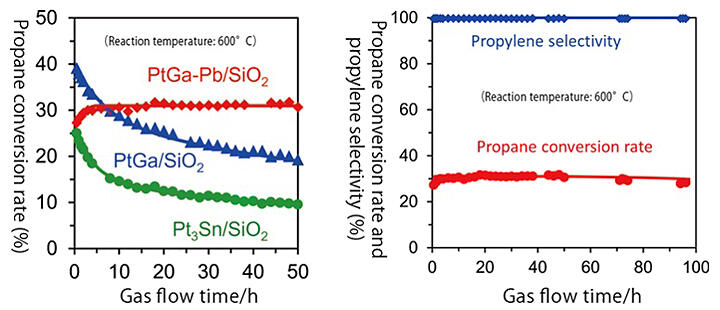
New face selection for reaction activation and inhibition: Five times more active with a cerium oxide base
After developing the three-element alloy catalyst for propane dehydrogenation, Furukawa began to work on synthesizing a new catalyst effective in the "propane oxidative dehydrogenation reaction" using CO2. In propylene production, the propane oxidative dehydrogenation reaction using CO2 as an oxidant has long been studied as a way to prevent carbon deposition on the catalyst surface. Recently, this strategy has been attracting attention as a means of utilizing and consuming CO2, a greenhouse gas, but it has not yet gone beyond the scope of basic research. "So, I decided to take on this challenge using multi-element alloy technology I had developed," he said, explaining his motivation.
In the propane oxidative dehydrogenation reaction using CO2, propylene, carbon monoxide, and water are produced from propane and CO2. Three key points regarding catalyst development in this reaction are: (1) selection of elements that activate propane and CO2, (2) suppression of side reactions, and (3) promotion of carbon combustion using CO2. In addition to platinum, which activates propane, Furukawa and his colleagues made new choices, cobalt for CO2 activation and indium for suppressing side reactions. Furthermore, for the base, instead of silica, they considered using cerium oxide, which is also used in automobile catalysts as a material promoting carbon combustion. New catalysts were designed and synthesized from these materials and evaluated in various ways.
These results confirmed that the new catalyst maintained high propylene selectivity for a long time. Furukawa and his colleagues analyzed the reaction mechanism in more detail and demonstrated that high activity, selectivity, and durability are achieved only when all four components (platinum, cobalt, indium, and cerium oxide) are present. Furthermore, in January 2022, "Pt.Co.In/CeO2" was announced as a new three-element alloy catalyst for the propane oxidative dehydrogenation reaction for effective CO2 utilization (Figure 2). This new catalyst exhibited the highest catalytic activity, propylene selectivity, durability, and CO2 utilization efficiency, especially for propylene production, which was five times higher than the previous highest value.
Furukawa spoke enthusiastically about the new catalyst, saying, "Not only can it be manufactured using similar methods and at the same cost as conventional catalysts, but we can also expect it to enable the practical application of a new industrial process for the oxidative dehydrogenation of propane that combines highly efficient propylene production with the effective use of CO2." These results have been passed on to A-STEP industry-academia collaboration (fostering type), and research is underway to further develop innovative multi-element alloy catalysts and their practical applications.
Figure 2:Structure and role of the "new catalyst Pt-Co-In/CeO2"
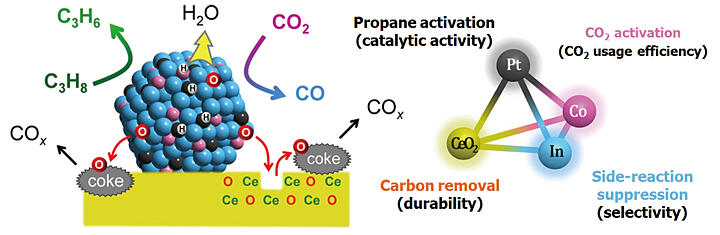
Introducing an orderly structure for high functionality and working to promote the use of hydrogen
The number of elements in alloy catalysts can be increased to five or six to achieve more precise and advanced functions and characteristics in a stable manner. Most ordinary alloys have a disordered structure. However, Furukawa and his colleagues introduced an ordered structure into multi-element alloys that they are researching, allowing them to exhibit high performance as catalysts. The aim is to further improve performance by partially replacing this with a "high-entropy intermetallic compound" (Figure 3) that contains even more elements.
In fact, the researchers confirmed that the three-element catalyst for propane dehydrogenation developed in 2020 maintained stable performance for more than two months by evolving into a six-element high-entropy intermetallic compound. In the future, Furukawa hopes to achieve even higher functionality and longer life for propane oxidation and dehydrogenation catalysts using multi-element technology. Simultaneously, he hopes to improve the economic efficiency of propane production by reducing the use of expensive metals, such as platinum.
Parallel to this research, Furukawa's laboratory is working on developing catalysts that will enable the effective use of not only propane but also ethane, butane, and methane as well as catalysts that will promote CO2 and hydrogen utilizations. Furukawa says he feels that opportunities for catalyst researchers are increasing in response to rising global environmental awareness. He is pushing forward the practical application of new catalysts through collaborative research with companies and other means to complete A-STEP. Their research will contribute to realizing a decarbonized and clean energy society.
Figure 3:Image of the high-entropy intermetallic compound
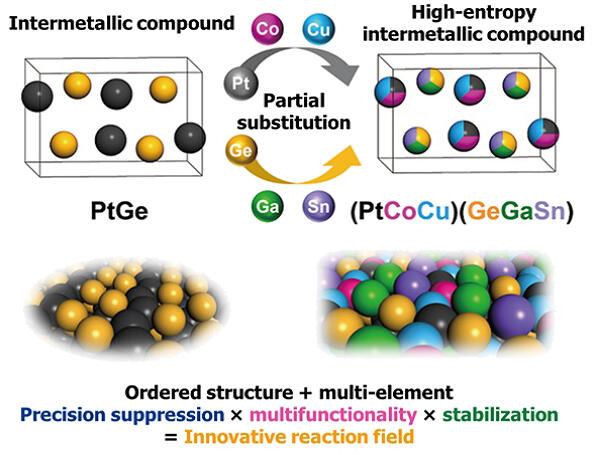
(Article: Shinji Moribe, Photography: Hideki Ishihara)